I’m in the Montebelluna area of northern Italy, far from the alpine mountains (as central European distances go, anyway) and immersing myself in the business side of backcountry boots and shoes. Dynafit and Scarpa are my hosts. I’ll give Scarpa time first since I’ll be doing major Dynafit coverage over the next days due to their annual product launch (heading back up north to Praxmar, Austria for that, near Innsbruck). Today, the more traditional part of the alpine shoe business: That of climbing and hiking footwear.
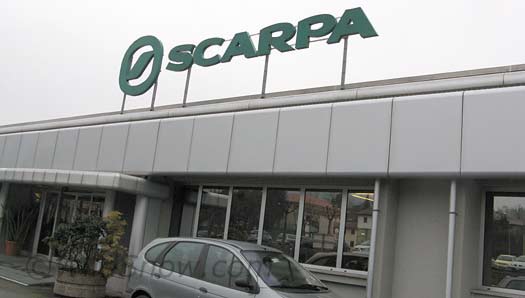
The Montebelluna area (see map below) varies from quite industrial to outlying areas that a tourist would find enjoyable. For example, I'm staying in your classic country inn about 15 minutes from here, an ancient farmhouse that's been modernized inside but still has its old walls, surrounding animals and vineyards, stuff like that. The Scarpa HQ in this photo the larger and more recently built of their factory buildings in Asolo, a more classic town outside of Montebelluna.
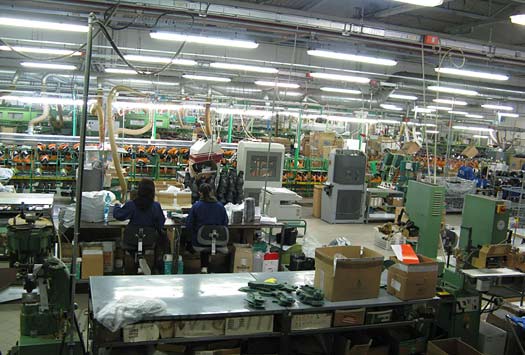
Scarpa factory is well used, but clean and neat with of course many diligent people getting it done. This building is mostly climbing boot manufacture from start to finish, with a section in the back devoted to ski boot final assembly.
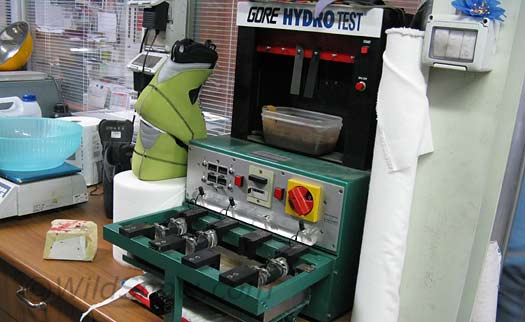
The Gore Hydro Test machine is one of the mandatory processes you have to apply to your materials so you can obtain and use Gore products. It measures how much water the boot's materials absorb. Too much water in the leather or fabric, and hydraulic pressure while you walk will force the water through the Gore membrane. So it's pretty important that notwithstanding the actual Gore membrane, boots are made of fairly waterproof non-absorptive materials.
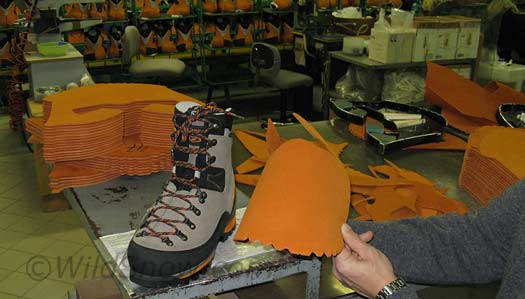
Now, into the process of making boots. First step is cutting numerous parts of the raw materials. In this photo, on the right is the piece which forms the upper, left is a finished boot of a different color. It's impressive to see how a bunch of what appear to be scraps quickly become a brilliant alpine climbing boot. Apparently they make a few hundred thousand shoes and boots a year.
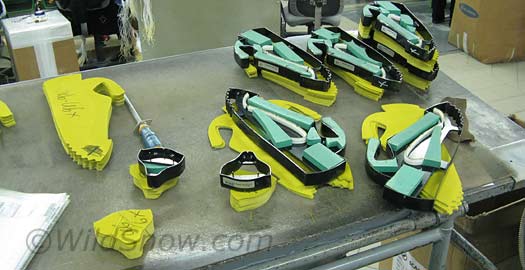
Most boot parts are cut using dies (shown) in a die press. Most of this cutting is automated, some more of a hand process due to variations in materials such as leather that it takes a 2 million euro machine to catch, or a human hand and eye. Walls near this area are covered with thousands of carefully labeled dies for myriad boot models and parts. Can you imagine loosing just one die, talk about a holdup! Probably the most interesting thing about the 'artisan bootmakers' of Asolo is seeing how they mix hand work with automation. You can tell boot making robotics could be taken to the nth degree, but it's nice to see a few humans involved in more than punching buttons or clicking a mouse.
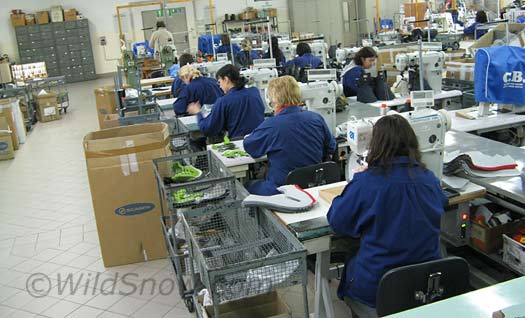
Scarpa has about 160 employees in Asolo and Romania, that's down from several times that during days of less automation. Still, as for example in this photo, some tasks may be better suited for the human eye and hand (these guys are sewing various small parts inside the boot upper).
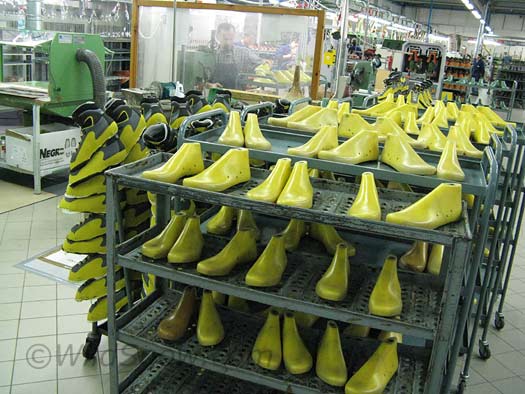
The magic of boot and shoe making is in the last, a carefully sculpted shape that is used as a form to mold the boot over. To manufactured lots of boots, you need lots of lasts. So they make one master for each size, then mold a bunch from that, resulting in thousands of last feet 'kicking' around the factory on racks and shelves. It looks kind of surreal. Adding complexity, Andrea told me that in some cases they make a European, North American and Asian last in each size, and thus shape boots according to what part of the world they're going to because the average foot shape tends to vary with the greater regions.

Big step, boot uppers are ready to placed on the lasts.
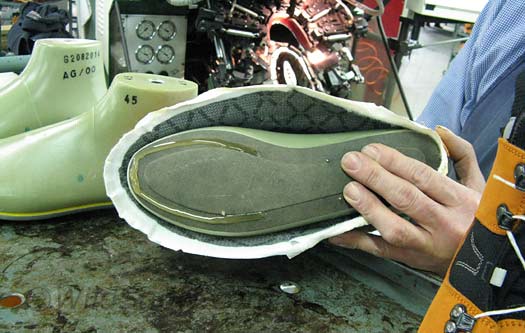
Prior to final steps in making a hiking or climbing boot, the last is inserted.
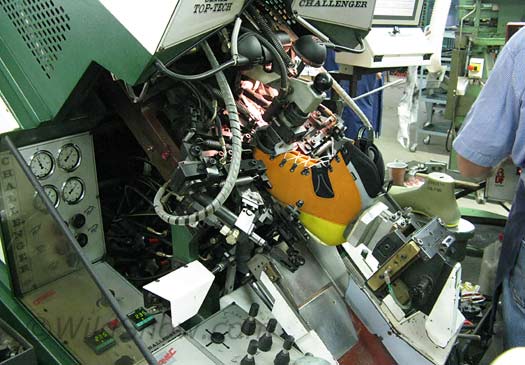
This octopus looking machine stretches the boot upper over the last and turns the edges underneath the sole area, where they'll eventually be buried by the boot sole. I'd imagine that when done by hand 70 years ago, this process was one reason they only made 6 pair of boots a day, instead of several thousand.
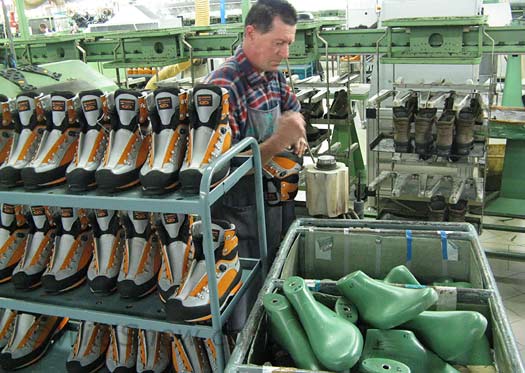
Just about done. The sole is applied, the whole boot is pressed in a device called a 'water press,' then the last is popped out. After that a few details such as laces are taken care of along with a quality control inspection, then into the box they go for your perusal on the store shelf.
Next visit to Scarpa we’ll check out the ski boot making, which is actually quite simple from a labor standpoint compared to mountaineering boots. Meanwhile, I’ve got to get some bloggin’ in the pipe for Dynafit as well! Fun stuff.
Shop for Scarpa ski boots here.
WildSnow.com publisher emeritus and founder Lou (Louis Dawson) has a 50+ years career in climbing, backcountry skiing and ski mountaineering. He was the first person in history to ski down all 54 Colorado 14,000-foot peaks, has authored numerous books about about backcountry skiing, and has skied from the summit of Denali in Alaska, North America’s highest mountain.