It’s easy, buy a Fiberforge Relay fiber assembly machine for a cool 1.2 mil, add a 450 ton press with heat welding capability and custom made mold, and you to could have a pair of planks that cost about a million each for serial number one.
How do I know this? You can make fun of us saving a good 3 pounds of weight on Denali by bringing carbon fiber stove boards for the group. But composites are cool. So knowing that cutting edge thermoplastic composites company Fiberforge exists just down the street from here, we thought we’d pay a visit and see what we’d need for the garage to make the WildSnow custom ski (stoveboards, how 1990s!).
Production manager Colin C. showed us around, check it out. (Please note, Fiberforge’s manufacturing processes and machinery are patented and proprietary, we were thus careful in this post to publish nothing more detailed or revealing than can be found in the Fiberforge public website.)
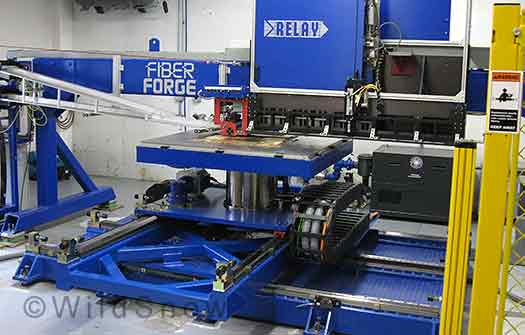
The foundation of the Fiberforge process is this machine that lays up and thermal tack welds standardized fiber strips (carbon or other) into sheets that are then molded. What makes this stuff terrific is that no additional resin is used in the assembly and molding process. What's more, these machines are optimized for mass production. No mess, way less weight, hundreds of widgets getting made.. Hence the possibility of a carbon fiber ski that could beat Goode at the weight game.
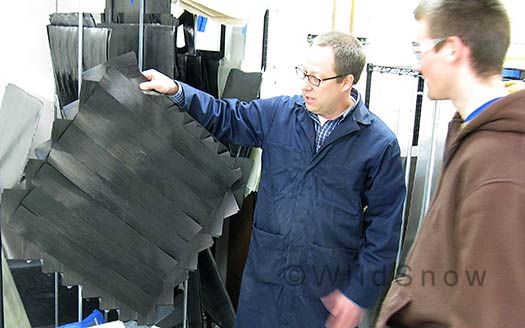
Colin shows us the layed up sheet that comes out of the Relay machine. This material then goes to the 450 ton heated press forming system, which is where the real magic happens. According to Colin, while some shapes can't be molded with this process, a vast variety can be, and they end up with a greatly enhanced strength/weight ratio in comparison to traditional fiber/resin layup techniques. Seems to me they could make skis.
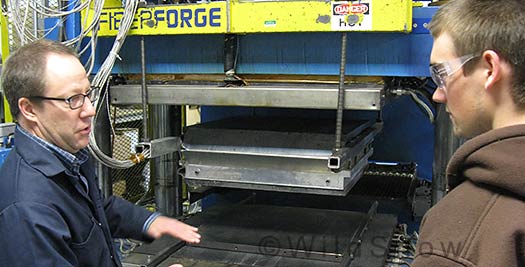
The heated 450 ton press. This thing takes so much current they have to run their own gigantic diesel generator or they'd black out half our county.
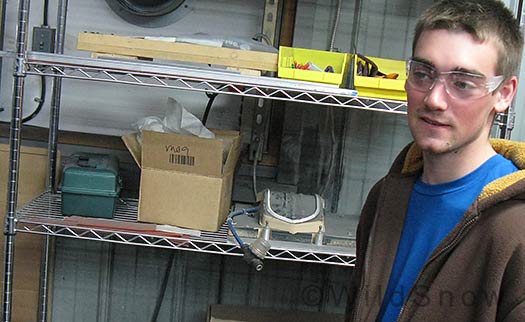
Fiberforge is not unfamiliar with outdoor products. Somewhere in this photo is the mold for the Mystery Ranch backpack framesheet. They've made more than 20,000 of those guys, which perform much better and are lighter weight than the now traditional poly/alu/fabric framesheets used in many of today's backpacks.
In all, a truly interesting factory visit that did get Louie and I thinking about how whole bunch of outdoor products could be substantially improved with Fiberforge technology. Thanks for the tour Fiberforge! And the eternal question, will these machines fit in my garage? Shoot, I have to throw away my shop vac to make room!
WildSnow.com publisher emeritus and founder Lou (Louis Dawson) has a 50+ years career in climbing, backcountry skiing and ski mountaineering. He was the first person in history to ski down all 54 Colorado 14,000-foot peaks, has authored numerous books about about backcountry skiing, and has skied from the summit of Denali in Alaska, North America’s highest mountain.