While overall the world of ski boot making does seem a bit stagnated, when it comes to making individual products that compete in a given arena, it may only look boring on the surface. Consider the Dynafit Evo. While visiting Dynafit in Montebelluna Italy this past January, I was blindfolded then led to the inner scriptorium of their boot creation department. Not doubt they sterilized the place of models still in development (bloggers, we’re like vultures), but they had all the cool Evo and Zero series proto patterns laying around, and were willing to talk about boot making as long as my notebook paper lasted.
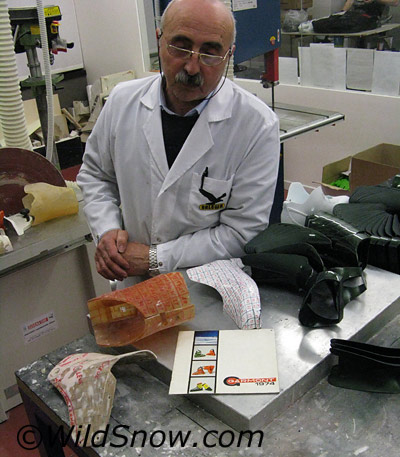
Back in 2005 when parent company Salewa decided to launch Dynafit bigtime as a 'vertical' product line, they knew they needed boots that worked. Before then, it had been hit and miss, with a few winners (TLT), but losers such as Aero. So what they did was go out and find one of the best boot designers in Montebelluna, and hire him. Mario Sartor is his name, and he's been designing ski boots since working on various Garmont alpine models in the early 1970s. Yep, that book on display is a 1974 Garmont catalog, and Mario is responsible for nearly everything in it. What a contrast, on the left are developmental parts for the new 2011 Dynafit Evo boot, probably the most high-tech and lightest weight shoe they've ever produced.
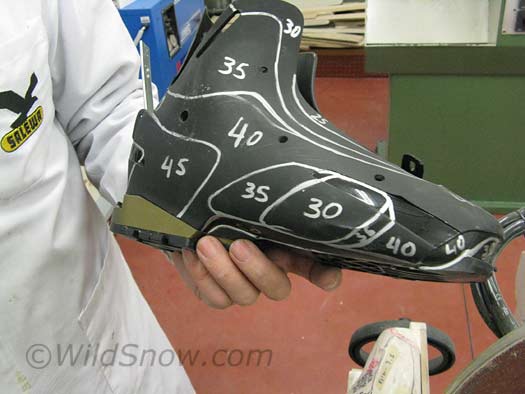
When developing a boot, while computers may be involved, these guys do much of the work by building patterns made from wood wafers and resin (that's what the brown cuff shaped thing is in the photo above). After they get it close, they start working on the actual mold, then tuning the plastic thickness. In this photo, a developmental molding of the ZZeus is marked for necessary thicknesses in different areas..

ZZero provisional molding with detail dimensions for each square centimeter. Such attention to plastic thickness is essential to building a boot that flexes 'sweet' and is still light and supportive. It is more art than science.
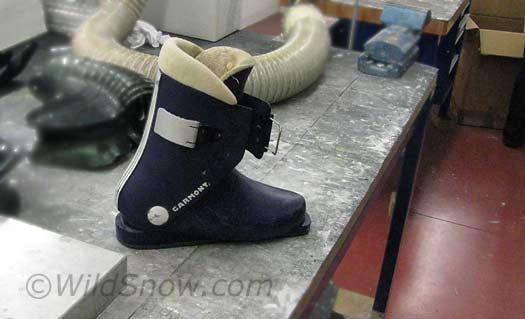
Mario designed this 1974 Garmont rental boot. I actually experimented with some of these for ski touring back during that era. What's interesting is that the concept of a boot molded from stiff plastic, with a minimal number of buckles, is the idea behind Evo -- but was being done back in 1974 with a rental boot. Cool to see this concept taken to the limit with Evo, but on the other hand, what was I saying before about boot development happening rather slow?
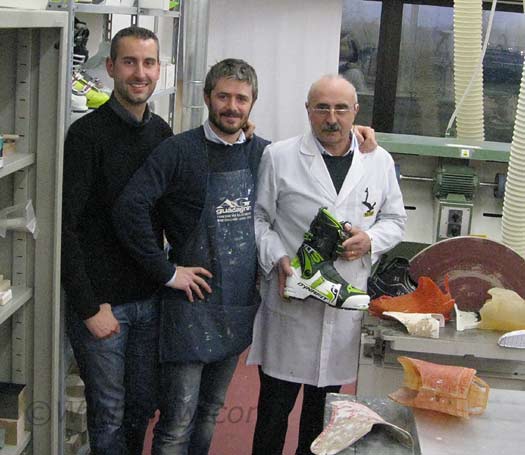
Dynafit brain trust responsible for development of all the new shoes. Left to right, Federico Sbrissa, Pierro Feneto, Mario Sartor with their last masterpiece. It was quite an honor to speak about ski boots with an icon such as Mario.
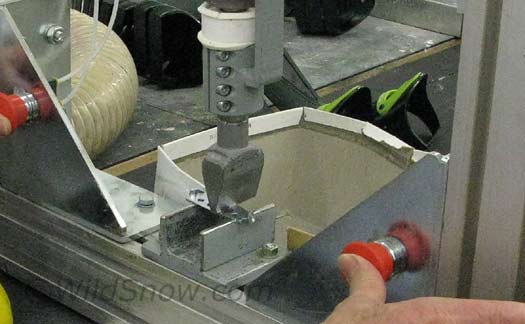
This thing is cool. It's a hydraulic anvil they run all the boot toe tech fittings through to make sure they're plenty strong. In the photo, that's a tech fitting being slammed by the anvil. Like anything light and minimalist, tech fittings have to be carefully made and fully tested as the margin for error is low.
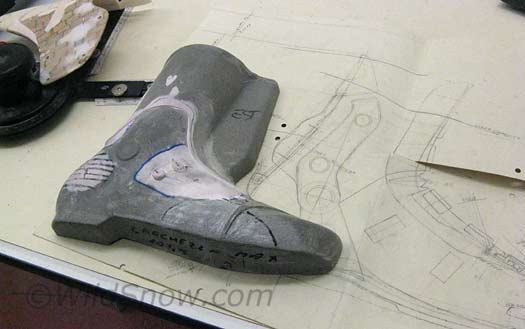
This is the interior shape of the boot, known as a 'last' but in this case more of a precursor to what the mold interior is going to look like. The hand drawings are pretty cool as well when you're used to seeing so much computer stuff. Those are Mario's work.
What fascinated me about this process is it’s mostly done in a fairly small lab/workshop, by just a couple of skilled craftsmen. Of course, after they have the shapes they want, the huge aluminum molds are made somewhere else — to the tune of around 100,000 euros per size! And before that, Mario and his guys have to figure out all the buckles and such, then extrapolate all the different sizes from their master design (which is usually a 27). In all, a stunning amount of work goes into those ski boots on your feet.
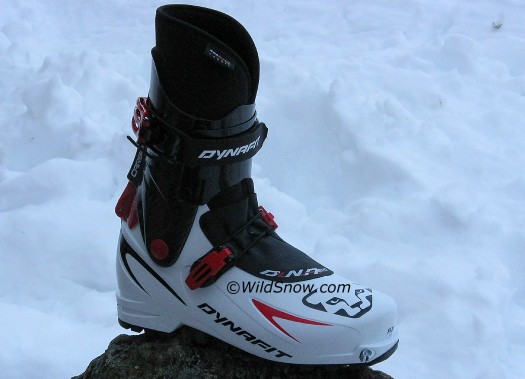
And of course, what they've been working on, the Dynafit Evo. Out next season.
WildSnow.com publisher emeritus and founder Lou (Louis Dawson) has a 50+ years career in climbing, backcountry skiing and ski mountaineering. He was the first person in history to ski down all 54 Colorado 14,000-foot peaks, has authored numerous books about about backcountry skiing, and has skied from the summit of Denali in Alaska, North America’s highest mountain.