G3 wouldn’t let me check out their climbing skin assembly operation during our recent visit to their Vancouver headquarters. “Secret processes” was the story. Not to worry, just learning they basically start with skin fabric and come up with a full line of furs right there in their facility. That is enough to impress. I mean, how cool? Want to try a different glue forumlation? Have the chemist whip it up, smear on a pair of skin, then take a short drive out of town and do some testing on Mount Fromme or Crown Mountain. Fortunately, while even my hidden spy cam couldn’t penetrate the climbing skin room, G3 engineer Rob Moore did show us enough other stuff for photos and comentary.
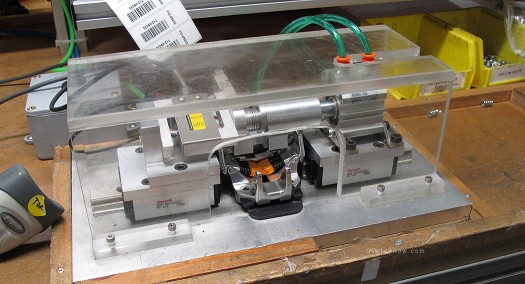
Toe unit tester for Onyx backcountry skiing binding. This rig tests the 'pinching' force of the toe wings, which needs to be reasonably consistent to insure the binding's safety release and retention work as expected. Rob told me that just a small metal filing or dirt getting caught in the mechanism during manufacturing can change things drastically, so serial numbering and testing _every_ binding is, in his view, essential to providing people with a quality product. From what I've gathered over the last few years, this type of individual testing is essential to the type of binding indemnification that ski shops need to protect themselves from liability issues. Also, perhaps it's something that'll be necessary for the ever illusive TUV certification of the Onyx bindings to ISO standard 13992?
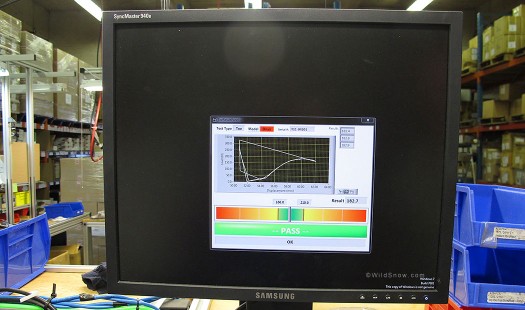
Binding test results for one particular serial-numbered toe unit. The idea is they have an ideal profile, and each binding has to match it within a certain tolerance. What's impressive is they test _every_ binding and keep the results on file. Not all binding companies do that.
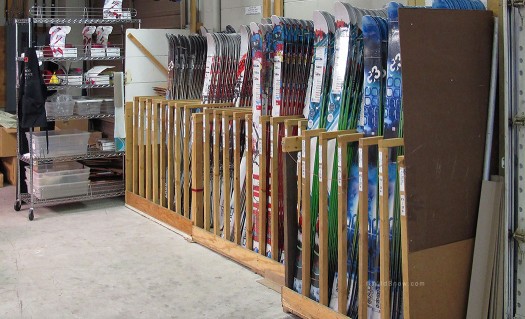
Skins and skis being readied for shipping. As with many other companies, G3's product manufacturing constantly evolves to a mix of in-house work, actions elsewhere in Canada, along with the usual Asian component.
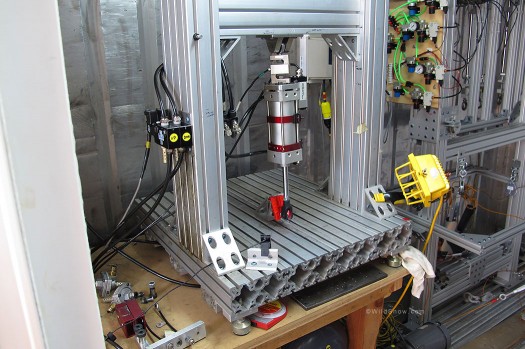
My favorite part of the G3 facility is their cold room. They created this space out of a refrigerated shipping container, which when you think about it is the perfect way to instantly create an effective walk-in freezer. Add a few testing machines like this one, and your'e ready to rock -- or crack. In this case, the heel lifter for a tele binding is being 'used' thousands of times, in the cold. Rob showed us a bunch of other contraptions used to simulate real-life abuse, but admitted that no in-house testing can totally simulate real-world use since forces in the field are complex and hard to totally duplicate.
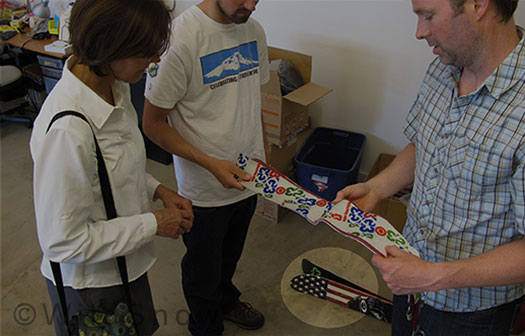
Bonus spy shot. The skis peeking out from behind Rob (who is showing us the High Traction Skins) possibly a test pair of their new super-lightweight plank, to be introduced during winter trade shows. The graphics are provisional, of course, just something they appeared to be having fun with. If I say more than that G3 will make me do a 50k nordic race on their High Traction Skins, so mum is the word. But they did look like VERY interesting skis. That in light of the fact that at least two or three other companies are attempting to main-stream manufacture and retail modern width backcountry skis that weigh around or under a kilo each in 'normal' lengths. I guess I should add that due to this, some people's wallets will probably become lighter weight as well.
WildSnow.com publisher emeritus and founder Lou (Louis Dawson) has a 50+ years career in climbing, backcountry skiing and ski mountaineering. He was the first person in history to ski down all 54 Colorado 14,000-foot peaks, has authored numerous books about about backcountry skiing, and has skied from the summit of Denali in Alaska, North America’s highest mountain.