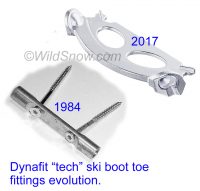
Thirty years of design engineering, ski touring tech fittings were the result of one man’s vision, and are now an industry wide informal standard. Click images to enlarge.
The revolutionary design philosophy of the first “Dynafit” ski touring binding system, introduced around 1985 and then known as “Low Tech,” was a configuration eliminating the usual frame type touring binding. Frame bindings used various contraptions or “carriers” to allow the boot to be latched down for downhill or freed for walking. Instead, the game changing Low Tech system required a toe and heel fitting built into the boot — thus using the boot as the “frame” or “connector” between toe and heel.
The system was significantly lighter than nearly any other ski touring binding of the time, and had better walking ergonomics as well (due to the walking pivot being closer to the natural “pivot” of the human foot).
While “tech” bindings caught on slowly at first (they appeared tiny and fragile) the slow march to world domination was as inevitable as the rising sun.
The heel fittings were relatively easy to make and attach to the boot, while the toe fittings have been subject to a number of evolutions.
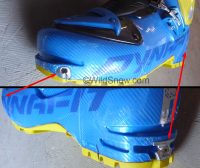
Basics for those of you new to ski touring gear. Dynafit tech fitting equipped boot with QSI (Quick Step In) toe fitting and standard heel fitting. Click to enlarge.
Mounting a binding toe fitting in the boot was not easy. Inventor Fritz Barthel went through numerous iterations. A few of his attempts in the photo below, and explanations from the man himself.
#1 in photo: “Drilling through a finished boot into an inhomogeneous mix of different materials (rubber, plastic, air) is not really feasible with good results. Plus you open the inside of the boot shell and a quite big part of the steel cylinder is extending into the toe box and thus demanding space and creating a heat bridge with cold getting into the shell. I used this method for the first Low-Techs with the Dynafit boot and previously for the Koflach – Ramer prototype.”
#2 in photo: “Reducing the diameter of the rod plus offsetting a plate from the center-line to avoid the internal opening of the shell. Hmmm, as the boots had already the sole glued on I had to try to peel it off again. Then grind a cavity out of the plastic and with the help of some kind of gauge melt in the heated insert into the plastic trying to get some of the plastic through the holes and cover the piece with additional molten plastic. Glue on the sole again. How could I ever believe this could work! Anyway, some of the boots lasted a while but at the end every single one of them disintegrated. Total disaster, so sad!”
#3 in photo: “First attempts with precision cast parts. The first few pieces were made with a handmade master which was put into a silicone mold to get the wax models for the casting. I was asking a goldsmith who was using precision casting for making raw parts for his rings and jewelry. He could only use soft stainless steel which could not be surface hardened. So the wear was high and the time of use very limited. But Dynafit let me try to get that piece in-molded during the boot shell plastic injection. The risk was high to destroy the shell mold, with high costs of repair. But we managed to make a few boots to check if the stability of the insert was sufficient. The procedure to hold the insert in the right place inside the mold and prevent it from loosing the correct position when the plastic is injected with high speed and pressure is still — even today after numerous different methods of clamping and positioning — a tricky thing.”
#4 in photo: “More or less how the toe insert is today.”
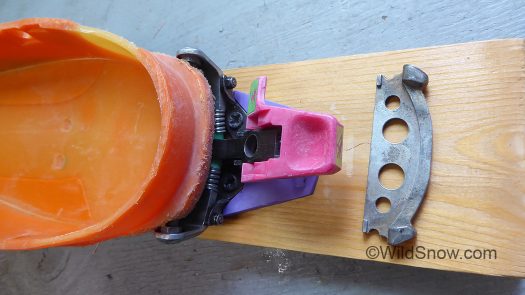
1980s boot toe with early Dynafit binding, fitting extracted from that era boot displayed to right.
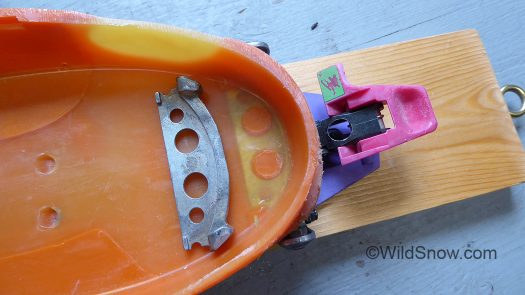
Boot toe showing the molded fitting beside a fitting as it appears before being molded.
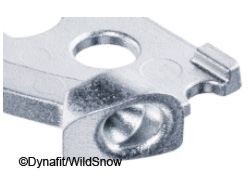
Early Dynafit tech insert (toe) remained virtually unchanged from 1990 to 2008, when the Quick Step In was introduced.
As detailed in the Barthel photo above, early boot toe tech fittings, from 1985 to about 1988, had larger but similar shaped sockets to receive the binding toe pins. The boot fitting was manufactured as a tubular steel slug that was inserted into the boot toe after the boot was molded. These proved problematic (they loosened in use), and when the Dynafit brand acquired manufacturing rights around 1990 they changed the shape of the toe fitting and began fixing it into the boot toe during the plastic injection molding of the boot — a clearly superior method that’s proved to be quite robust.
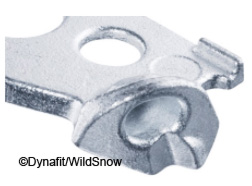
Quick Step In (QSI) fitting makes entering tech bindings easier.
While the hidden parts of the fittings have remained virtually the same, in 2007 Dynafit introduced their “Quick Step In” (QSI) fitting. With an added lead-in notch on the lower portion of the socket, the QSI eased the challenge of clipping into the binding — especially for skiers new to the system. While heavy users of tech bindings get used to snapping their boots in, newcomers to the sport, or people challenged by adverse conditions (such as entering the binding in the dark, or with heavy snow or ice obscuring the mechanism) definitely do experience a “pain point” that begged a solution. Further, the boot fitting patents had expired. By freshly patenting the QSI, Dynafit sought to protect their investment in the Low Tech system.
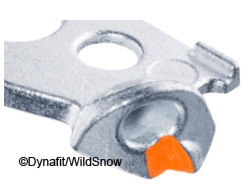
Only change with QSI is a lead-in notch or cutout, remainder of fitting is virtually the same as previous.
Here at WildSnow, we like the QSI but immediately noticed a downside. The fitting is thicker from bottom to top, leaving less room for ski boot sole rubber. Skiers who spent a lot of time out of their skis, perhaps scrambling rocks while doing alpine routes, experienced quicker wear than they were accustomed to. Still, the QSI was viable as most ski tourers don’t hike or climb much in their boots, and the early style fitting was still available in numerous boots if you did need it.
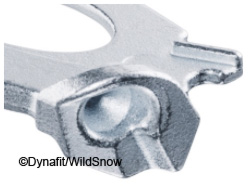
Master step fitting. On first glance not much different, but note the extra bit of steel above the socket, as well as a deeper incut.
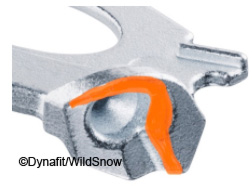
Masterstep with changed portions marked.
Enter Masterstep. Kudos to Dynafit. Think about what they’ve done over the past 20 years or so. It couldn’t have been easy bringing dozens of innovative — if not ground breaking products — to retail. To say they put a new face on ski touring is an understatement. They nearly morphed it into a new sport. Or perhaps they actually did. Sure, not all those wild product intros were flawless — some are best forgotten. The point is they were willing to base a corporate culture on innovation and fast response to ski touring trends. I get especially appreciative of what they’ve done when I consider that “Dynafit” is really just a brand, with disparate divisions working on each aspect of ski touring gear; a group in Italy on boots; skis prototyped and tested at major ski manufacturer facilities (currently Blizzard). I’m not sure the term “herding cats” has a good German translation, but I’ll bet the Dynafit CEO has an equivalent.
In any case, getting beyond my brief drop into fanboy zone, I indeed like the improved QSI “Masterstep” boot toe fitting that Dynafit began retailing this year. While it boasts a more pronounced lead-in notch, what I like is an effort Dynafit made to get more fitting steel present over the binding toe pins. The difference is only a few tenths of a millimeter, but every bit counts here as I’ve always suspected that deeper toe sockets would prevent certain modes of accidental release.
All well and good, but in the end, nearly any boot toe tech fitting will work for you if you learn how to use it. When you do so, enjoy the long wild history of how it all came about.
Burning question, what boots for 2017-2018 will be equipped with Master Step? Firstly, only certain models of Dynafit brand boots will have Master Step this season, and plans are vague as to when Master Step will be licensed to other brands. Scarpa will continue to sport the QSI fittings, while all other brands with Dynafit manufactured fittings will use the standard version. Dynafit boots with Master Step: TLT 7 and Beast, all versions.
(This post was made possible through the financial assistance of Dynafit. WildSnow.com created the post with 100% editorial control. Fritz Barthel contributed to the article, thanks Fritz!)
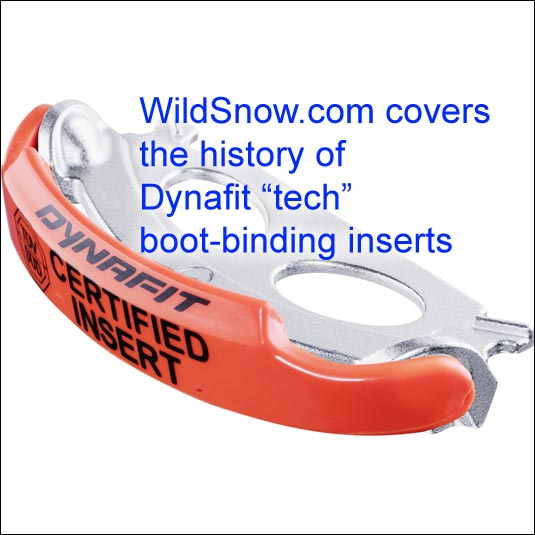
All boot fittings made by Dynafit come with this certification seal.
WildSnow.com publisher emeritus and founder Lou (Louis Dawson) has a 50+ years career in climbing, backcountry skiing and ski mountaineering. He was the first person in history to ski down all 54 Colorado 14,000-foot peaks, has authored numerous books about about backcountry skiing, and has skied from the summit of Denali in Alaska, North America’s highest mountain.