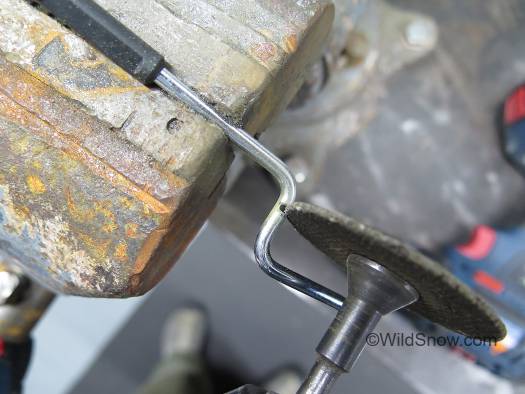
The brake has very little room at the bend where it enters the ‘cage,’ so I used a skinny cutoff wheel to make the cut. Most brake arms are somewhat hardened steel so an abrasive cut is much better than using a hacksaw. On the other hand, welding such steel weakens it, so the idea here was to “sleeve” it and locate the welds such that they didn’t weaken the arms too much.
It went something like this. I have a MIG welder, a nice new studio/workshop, and the desire to use 80 mm (officially 75 mm) ski brakes on my La Sportiva Svelte 96mm waisted skis. Sometimes you can simply swap the brake arms from a wider brake of another brand or model. The Dynafit Superlite 2 upper bend of the brake is shorter than most, so I couldn’t find an easy swap. Bending can add a few millimeters as can trimming off the sides of the plastic feet, neither an option in this case. (Note: various width brakes will be available for the Superlight 2, this method of brake width is presented as a way of fine tuning, or using what you’ve got, or to show a method of widening brakes with other binding models-brands.)
Best course of action appeared to be an additive process that involved cutting the stopper arms, adding a small chunk of 1/4″ tension pin as a connector, then burning a few tiny welds to hold things together. Clearly, this “5 wrench” rated project isn’t practical, it’s more a proof-of-concept and a message to Dynafit that wider brakes (or brake arms) would be nice. And it’s something fun to blog about. It as easy as brushing your teeth to remove and replace the Superlte 2 brake arms, so perhaps the aftermarket could step in with wider options if Dynafit doesn’t.
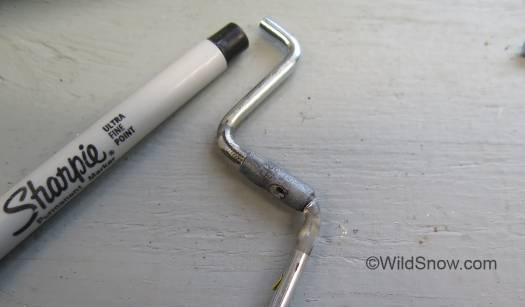
The better looking side of a welded sleeve, goal is to locate all welds on or inside the sleeve — I had mixed success with that since my welder wire and settings are really not fine enough for this type of work.
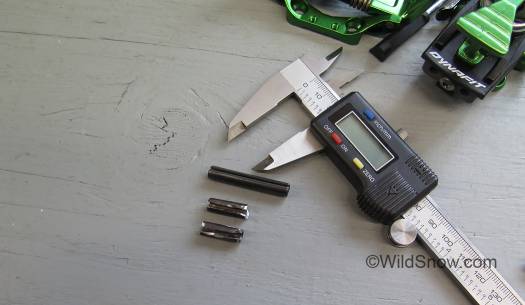
For sleeving I used 1/4 inch tension pins cut to length. They had a nice press-fit over the brake arm wire which held them positioned for welding.
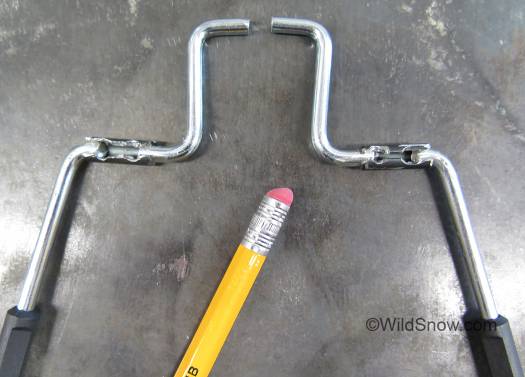
Brake arms with sleeve extenders. Arms that were initially wider would have more material to work with; these were difficult. The ragged looking stuff is where I opened up the tension sleeve so my .030 welding wire can get in there without just gluing the surface or blasting the brake arm material where it’s unprotected by the sleeve. Something more precise would work better. In case anyone is wondering, years ago I tried simply cutting and welding brake arms to a chunk of rod material. The arms are too thin and tempered for that kind of work; you have to sleeve them.

Publishing photos of your own welds can be like displaying your unclipped toenails, but sometimes things turn out ok. This was weld number 7 and 8. Practice helps. It didn’t help when my normal welding hat’s auto-darkening battery ran out and I had to use my flip-down. The welder is getting a bit beat as well but seems to do ok at lower settings.
WildSnow.com publisher emeritus and founder Lou (Louis Dawson) has a 50+ years career in climbing, backcountry skiing and ski mountaineering. He was the first person in history to ski down all 54 Colorado 14,000-foot peaks, has authored numerous books about about backcountry skiing, and has skied from the summit of Denali in Alaska, North America’s highest mountain.