They get to break stuff, make loud noises, and operate dangerous machinery. Who needs powder skiing?
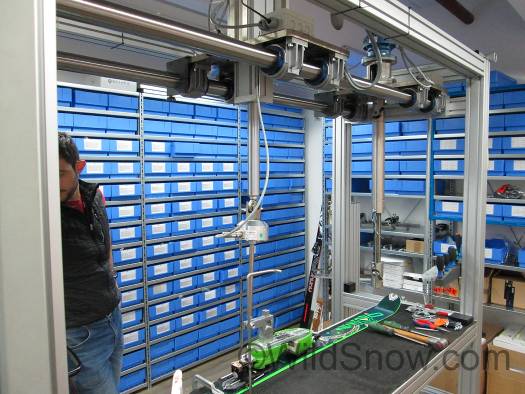
Much of the equipment here is intended to mirror how TUV tests bindings for certification to DIN-ISO standards. In this case, the binding release check and durability cycling machine releases the binding as many times as you care to set it up for.
The inner child is alive and well (can you hear that joyful laughter?) at the Dynafit Center of Excellence, a fancy name for the company’s quality control testing and analysis center near Munich, Germany.
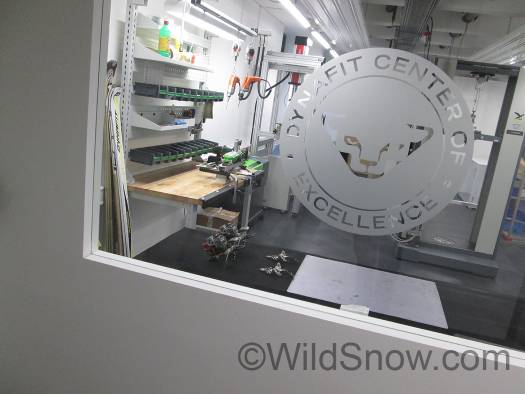
First thing you see is the logo on the workshop door. I thought this place was beyond cool and did smell like quality, but I also note that once a company hypes their quality control they’d better make good on it.
Dynafit always had somewhat of a ski gear test and prototyping center in Aschheim, Germany where their corporate offices are. But the facility was cramped and not modernized. They stepped things up in 2014, using former warehouse space to build a bright roomy system of interconnected workshops and offices that’s so clean you could make strudel dough on the floor.
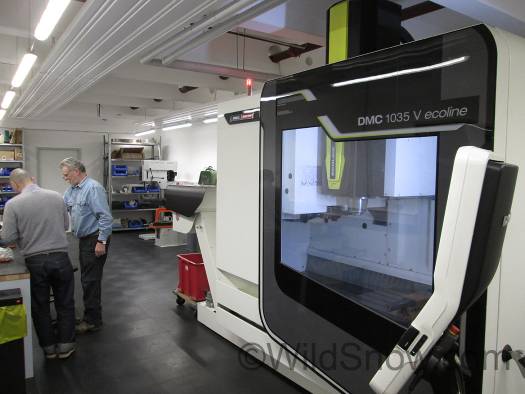
This is a test center as well as facility for rapid prototyping. Their 3-axis CNC milling machine is right there next to the entrance door. The joke is that every home workshop in the Tirol has a 3-axis, so why didn’t they get a 4, or a 5? A 3-axis is probably enough for prototyping, and a lot less money. I was told the previous time for getting prototype parts was three weeks or more; with in-house one of manufactured they’re down to one week.
Any legit manufacturer of products that involve personal safety needs to have a facility such as this, or pay a third party (time consuming and expensive) to do the work. In my opinion, testing to this extent has been woefully lacking in the ski touring tech binding industry and is perhaps still on the minimal side with some of the garage brands. But the big players had to step it up. Interestingly, the engineers will tell you that no matter what they do in the lab, things do happen once a product reaches the consumer. “We do our best,” they say “but nothing is perfect and it’s difficult to keep the quality control going all the way from prototype to the product you purchase in a store.”
A couple of things go on here, sometimes simultaneously with a given product, as well as being repeated for prototypes, pre-production “finished” units, and finally on a percentage of retail product to do statistical quality analysis and control (meaning you test a percentage of product from a given batch; if there is a failure recycle the whole batch.) For example, 10% of produced bindings undergo a complete test suite that’s an abbreviated version of the testing TUV does as well as some extra tests specific to a given binding. If any of the 10% have a problem then the whole batch is pulled.
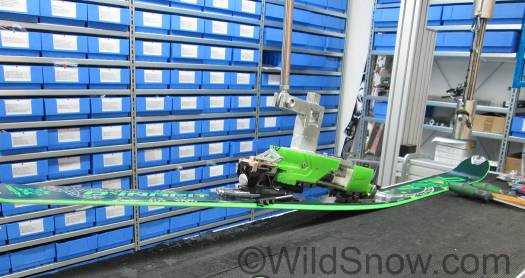
Engineers being engineers, I got a demonstration of why any classic tech binding is problematic. In this case, trapping your ski under a log is simulated. Due to the angles, the force required for release went up more than 30 percent, from about a 6 release value up to an 8. I don’t include this to be alarmist, only to show that the limited release testing done by TUV is somewhat crippled when it comes to matching real life situations. More, there is debate in binding testing circles about whether it’s best to clamp the ski and yank on the binding, or clamp the binding and yank on the ski.
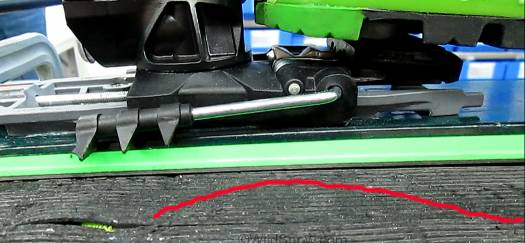
It’s known that with classic tech bindings, ski flex plays quite some role in how much release force the binding really requires to let go, as opposed to what you assume from the numbers printed on the housing. Here you can see the ski flexing up as the boot is pulled upward by the machine. A softer ski will flex more and allow the boot to come out easier. This is the ‘decamber” situation that with soft skis can also pull the binding heel pins right out of the boot fitting, or for example pull the pins far enough back to allow the now recalled Scarpa Evo Tronic actuator to slide in front of the pins (depending on exact adjustment of the binding.)
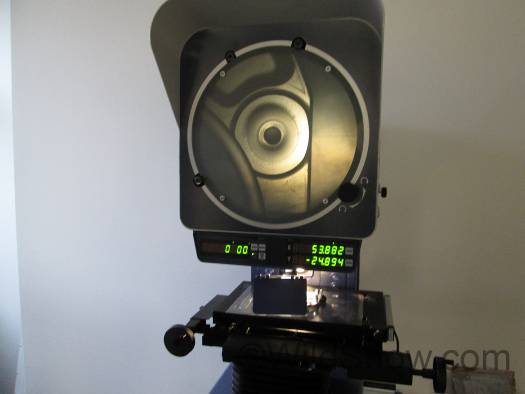
A big part of manufacturing is verifying manufactured parts by measurement to be sure finished products will function as intended. ‘Measuring and metering’ is done by three full-time workers. This machine is basic and effective. It greatly magnifies a given part, which you then measure by moving the cross hairs with knobs.
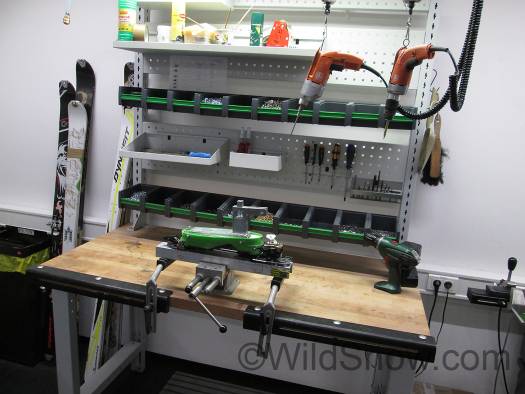
Nice workbench, but I did get the feeling it had been cleaned up a bit for my visit. The object on the bench is the ‘boot’ used for binding testing. Behind the boot you can spot some strudel dough they’re rolling out so thin and transparent you can read a Dynafit logo sticker through it.
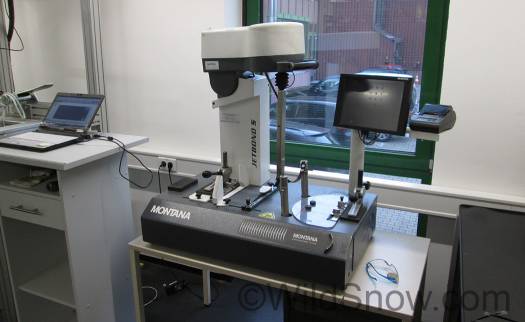
Montana release check machine is present as well. I was told that Dynafit is working with Montana to develop a system for testing tech bindings, as these machines presently don’t work very well due to the bindings having release at the heel and other factors.
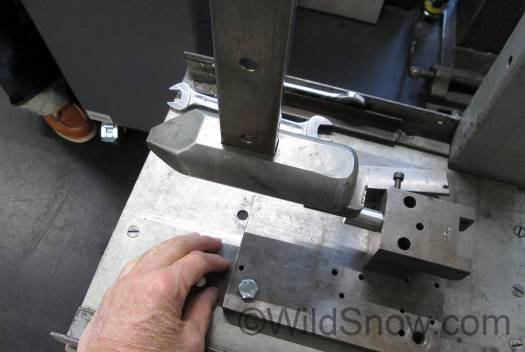
Last but not least, Maxwell’s Silver Hammer. Binding rear housing is placed on the spindle, the hammer is raised, and POW. See video above.
WildSnow.com publisher emeritus and founder Lou (Louis Dawson) has a 50+ years career in climbing, backcountry skiing and ski mountaineering. He was the first person in history to ski down all 54 Colorado 14,000-foot peaks, has authored numerous books about about backcountry skiing, and has skied from the summit of Denali in Alaska, North America’s highest mountain.