A long-awaited 1kg class boot from Tecnica, the Peak series, arrives on store shelves this fall. Cripple Creek Backcountry’s Doug Stenclik spoke with Tecnica group’s Product Innovation, Test Teams, Winter Validation lead Stefano Mantegazza, about the Peak’s debut and the long road from prototyping to a ready-for-market build.
The interview was conducted earlier this month and has been edited for clarity. Stefano Mantegazza is a longtime industry insider helping develop skis and boots so others can smile. All photos courtesy Stefano Mantegazza/Tecnica.
Doug Stenclik: From talking to folks at Tecnica/Blizzard North America, one unique aspect of boot designing at Tecnica is how quickly you can go from a prototype in the factory to testing on snow to be able to tweak the materials and the design. Tell me a bit about that.
Stefano Mantegazza: There are always many things to check to test as we develop prototypes, and that sometimes has to do with material changes in pre-production.
We are on the way where we can get snow with 3D-printed boots and ski. In the past, we did this with resin, which was a melted resin. We built the prototype boots in-house; this process was only for checking volume when we changed the shape. But these resin prototypes were not skiable because they were very stiff; we did this only to check the volume. Now with the 3D printed boots, in 20 hours, we can build a skiable boot shell. In the factory, we can check out the volume and angles and then build different liners. When we are okay with the basic setup, we can go on snow to test, and when it looks pretty good, we can create the first mold from aluminum. When we give the go-ahead to mill this mold from aluminum and get back on snow, it’s basically eight weeks.
You can read more about WildSnow’s Tecnica Peak coverage here:
—First Look
—The review
Doug: I remember a while ago at a trade show, some of the boot samples were 3D resin builds, and we could not handle them too much because they were so brittle. I know the resins have gotten better. So with a process like you described, where you are using resins, do you simply throw liners in that are sitting in the design studio rather than building out a new prototype liner for each resin mold?
Stefano: Yeah, because the resins shrink as they age day by day. So when you try with the same liner 10 days later, the boot shell prototype might be too small, or maybe my foot is a bit bigger or even smaller; that’s when you start to make mistakes. Now, with the 3d printed boots, hopefully, the shell sizes stay the same as they age. At Tecnica, normally, we prototype no fewer than 10 liners before we start to have a liner which is okay. For the new Zero G Peak series, for example, we produced more than 20 liner modifications.
Doug: For a long time, I imagined boot designers thinking about the liner as separate from the boot; you build the shell and then just put whatever liners are lying around. But now, it seems, the boots are designed with a liner in mind.
Stefano: Just for the liner modification with the Peak, we might just make small modifications, changing material, softer, harder, on the outside or the inside. We start basically with the liner design.
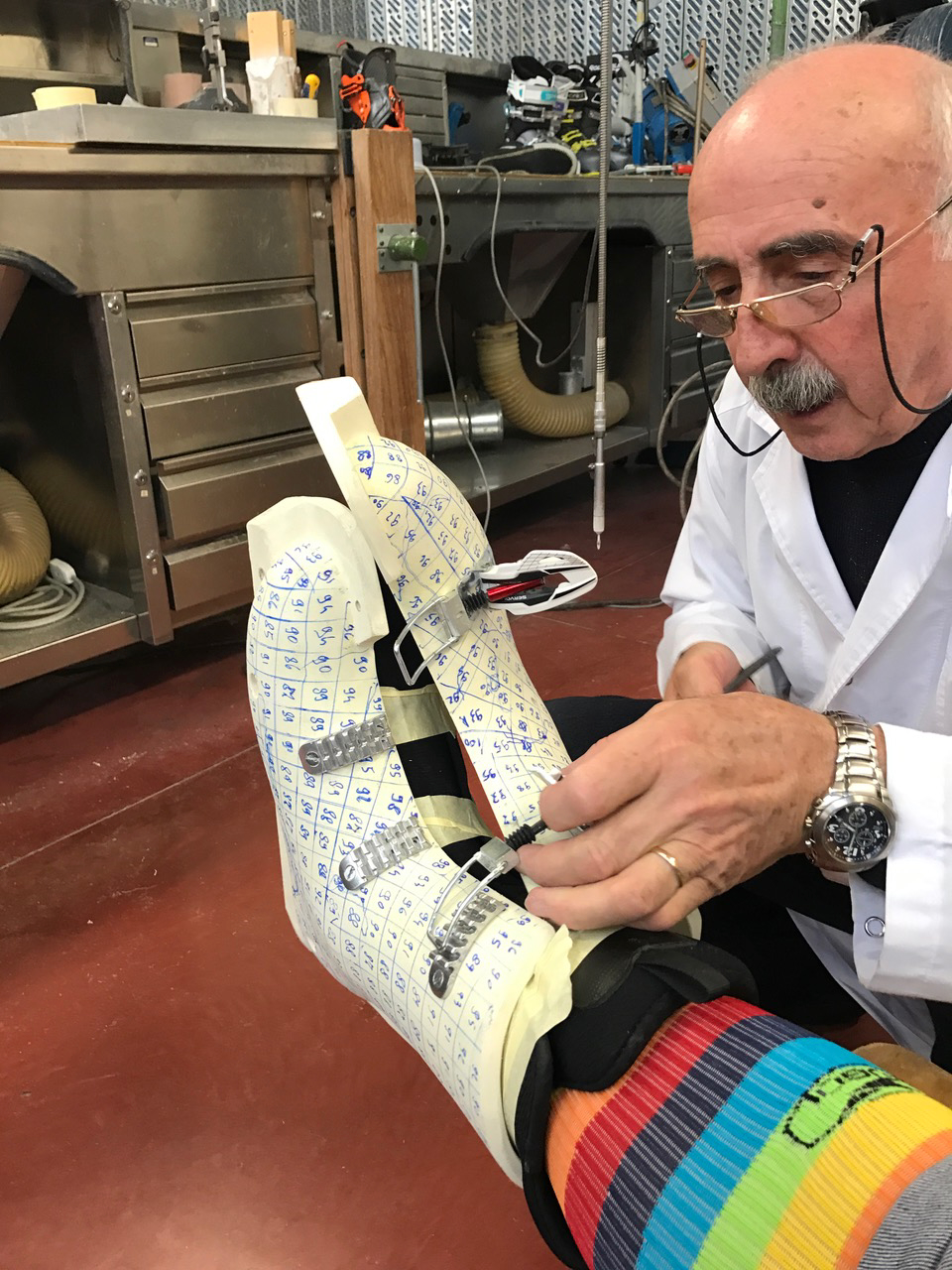
Two halves of an early iteration of the Peak. Here, Mario Sartor, a master of prototyping and developing lightweight ski boots, practices his art.
Let me walk back a bit and explain the process of designing the Peak. Basically, we started the Peak project with Mario Sartor; he is one of the oldest and more experienced ski boot designers, like a modelist or shaper.
We began with certain ideas about the liner; the liner should be around 200 grams. So we built the liner, which could have been better at first, but had an okay volume and thickness. Then we put the liner on my feet. And Mario created a clay shell around my feet, two halves, and then they were screwed together.
I then explained to Mario that the toe box was too small or to make more volume around the ankle or whatever. He gets to work opening up the two halves, grinding it or adding material, then closing it again, and so on, until he finishes the shape.
When Mario is done shaping, we scan it and get the 3D images into a computer. The interesting thing is that few people have the skills to shape a boot like that anymore; those that can grind and add material and complete the process by hand.
Doug: That is a very labor and time-intensive process.
Stefano: It is, and I think the Peak is the last boot we will see designed this way. Because now everything is designed by computer: so we take every boot, we cut it in half, we scan them, we take the volume, we take all the profile measurements. And then when we want to design a new boot, we can have our boots, maybe a competitor’s boots — we can overlay all the images, and you can see if it’s too tight here or there or too low. We can make the toebox a little bit higher, for example.
Doug: Do you ever see a point where all the boots will be 3D printed in the factory, or will we always use metal molds like we’re making boots with now?
Stefano: At the moment, this possibility looks really far away because it takes many hours to make many of the boots in the Tecnica line, more than 20 hours. It’s impossible at the moment. But that would be amazing because this is a complex process. For example, with the Peak, extracting the mold from the boots using the injecting process is very difficult because these materials are very hot, and the mold is in two parts, and we must pull the mold away from the boots. These molds are expensive too for each size.
Doug: As I’ve understood, it’s been a problem, for example, where a lot of women have size 21 feet, but nobody makes 21 boots, or at least none of those boots ever make it to the U.S. And the same, I imagine, if you have a very big foot, just because to produce an expensive mold would be price prohibitive if you’re only going to make 100 pairs of boots in a particular size.
Stefano: Exactly. The minimum for us in any size is 180. So we usually keep it in standby as we collect orders for a specific small or large size; if we have enough orders, of course, we say yes, but usually, the numbers are very low. In that case, we discuss it, sometimes really hard, because skiers say they need it. But sometimes the numbers are way too low, and we have to say I’m sorry.
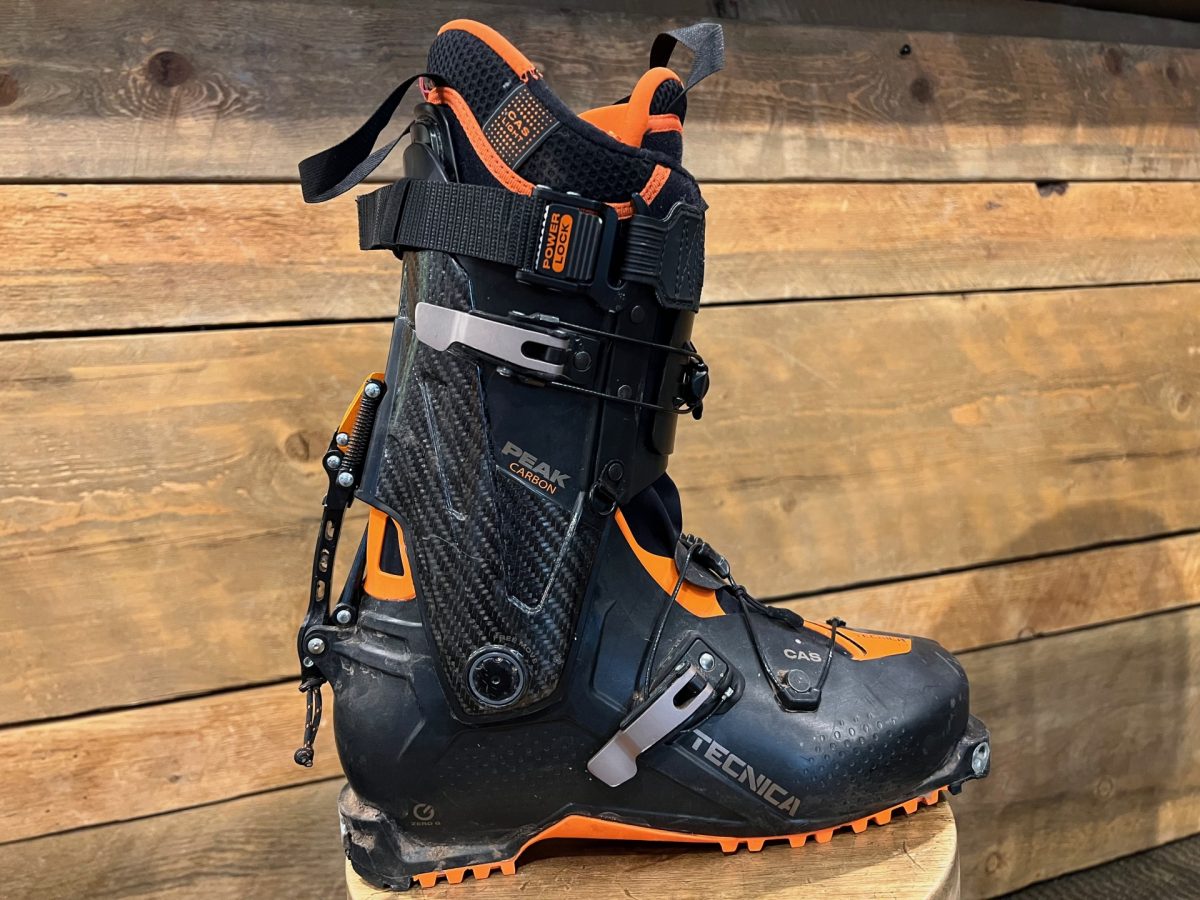
Tecnica went through eight molds and 20+ liner iterations in developing the Peak series of boots. The Zero G Peak Carbon is shown here.
Doug: Tecnica made a splash in the touring boot scene a few years back. Tecnica’s first big touring boot hit was the Zero G Guide Pro. I saw an old video of you showing that off, and that was probably about seven years ago, maybe a little longer—time flies.
Stefano: So that was really the beginning. Looking back 10 years to see where we brought Tecnica, we have to be pretty happy. The Zero G Tour Pro is now five years old boots. In Italy last week, that boot was once again the best boot of the year in its category from Skialper, which is an important buyer’s guide in Italy. It’s getting old that boot, but still, a good compromise in weight, how the boot hikes, and how it skis.
After a few years of the Tour Pro, we were trying to make a lighter boot; the marketing group and guides were asking. It was always our dream to build a below one-kilo boot with a lot of performance. Three years ago, we said, “let’s go,” and it took us two years to make it.
The first injected boot was 810 grams. For the finished boot, the goal was 960 grams. So the first injected boot was 110 grams heavier but needed to be better; it was great for uphilling, but then it broke. We had many, many problems. We ended up changing the mold eight times.
We usually add material, add material, make the prototype stable to prevent cracking, and more durable, and have the performance we hope for on the downhill. Let’s say it’s easy to make these boots lighter, but it’s difficult to make them light enough and perform with stability.
I see now that people are kind of scared because many light boots are good for uphill but downhill; they think you have to slow down, you have to use short turns, and you cannot really push more than what you would like. There is more learning and a long process to go through with lighter boots. When people understand that below one-kilo boots can ski well, fit well, and has the safety to go even faster, to ski wider skis, bigger skis, then the market can open up a bit more.
But many brands can now build better boots with plastics infused with carbon and other material advancements. With the Peak, we were surprised at how well those boots ski for their weight. We hoped to have a good downhill performance, but we were also shocked at how good it came out. The stability you have and the kind of flex you have is great, it is not a rigid block. Skiers should know it’s very difficult to make light boots with a nice progressive flex that is not too soft, which is not a block, but it works nicely.
Doug: Does the Peak series of boots have an adjustable lean for different settings?
Stefano: We have a spoiler, but it is not adjustable other than that. Having an adjustable forward lean would mean having more pieces and maybe some more problems, so we decided to go with a fixed position and for the feature set to stay solid and simple.
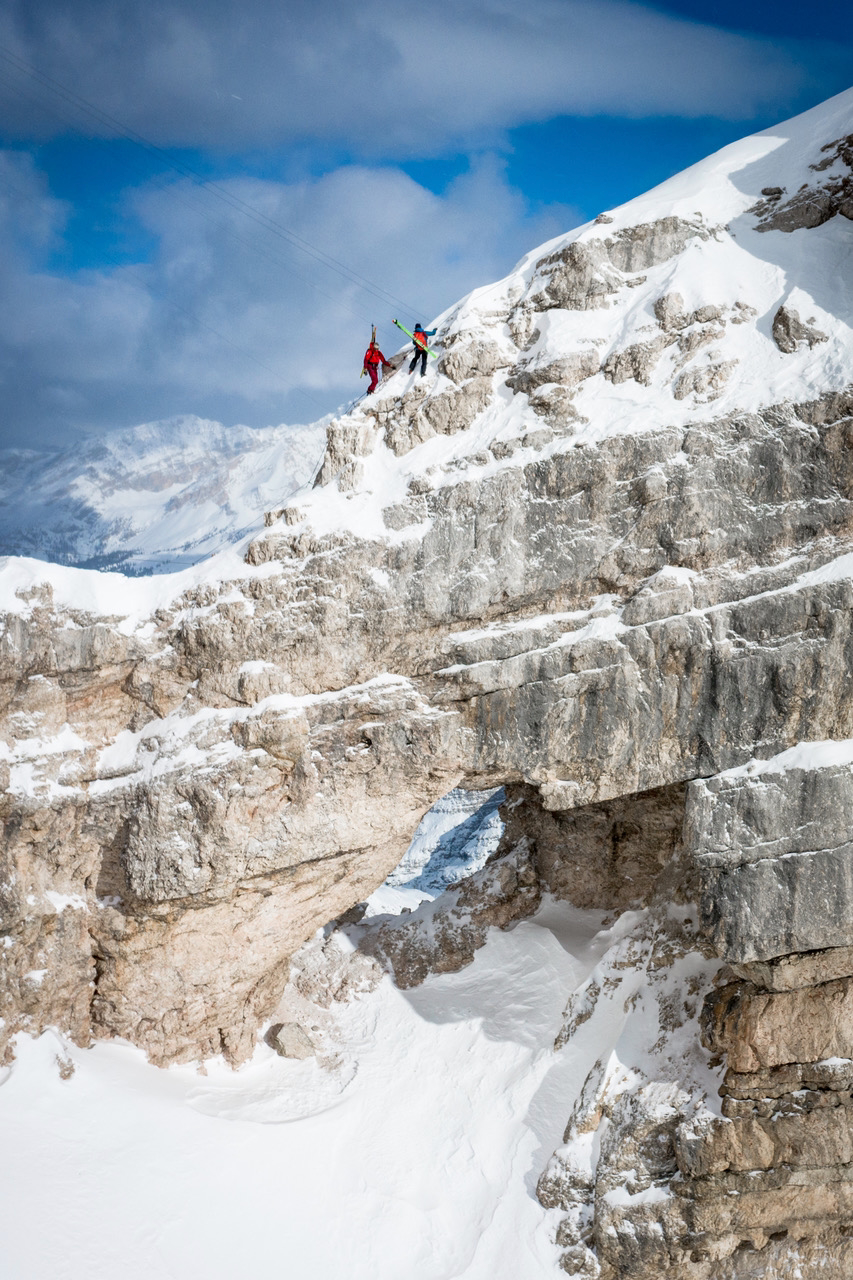
The awe of Italy’s high country – this terrain also served as the backdrop to test and develop Tecnica’s Peak series of boots.
Doug: You are giving us an idea of how complex it is to bring a lightweight yet skiable boot to market. Can you elaborate on how you got prototypes on snow and in the mountains during the Peak’s development process?
Stefano: It was a complex process, and with Covid, it took us one year longer than we planned. But the biggest on-snow help early on was here in Italy; we have three unbelievable Cortina-based mountain guides to help with prototyping. They bring a nice mix between mountain climbing and skiing and a racing background.
The process looks like this: I drive to Cortina whenever I get the boots or a prototype. The following day we are out with two or three boots and as many different liners; we go out many times to check the ski ability. At first, we do this on-piste using a lift. We compare boot to boot and mix in different liners to check the performance.
But as a 1kg boot, we need to test it off-piste. In the first year of testing, we had more than 100,000 vertical meters on the different boots. We underwent eight mold modifications, and as I said, from 810 grams, we ended up at roughly 960 grams. In the two-year process, we added thickness we changed the shell’s radius, but we made these changes step by step. We could have put more material in one shot, but we went slowly and carefully; that’s why it took us a lot of time.
During the first year of prototyping, I had 100,000 meters myself on the Peak and the following year, 70,000 meters — basically always with the Peak during those eight modifications. The three guides had even more time and vert. The prototype boots were in Svalbard, Norway, Crete, Siberia, and all over. Then when the boot was about 95% done, we made 40 pairs in January and February; these were not the final boots, but we were close.
Then every country where we sell boots selected three or four “gurus,” and we sent the boots out. We got some good feedback for the last modification loop before the final production.
Doug: Well, I’m interested in how the liner and the shell play together. Like I said earlier, I think the liner is usually an afterthought for many boots. It’s very interesting to know a boot was started with a liner and built out that way. I experiment with putting a lot of different liners in my boots, especially my lightweight sub-kilo boots because you can make a boot much stiffer by using a thicker, stiffer liner. And you know, thinking about that from the designer perspective, which is not typical, normally designers are not skiing 100,000 meters in a single season, so it’s good to hear you’re considering that.
Stefano: The Peak liner is the first we make on our own. We bought all the machinery. We didn’t buy the liner from Intuition or Palau like we did at the beginning; now, we build our own. And I’m not happy with many of these liners in the ski touring world. When you make a 200-gram slot-liner, yes, it’s 200 grams, but I would like to have in the future a liner that is 200 grams, and it can last for two seasons. But at the moment, at least from the knowledge we have, and we have in Italy around Montebelluna, many small factories are working for the ski boot industry, and the material we would like to use for liners does not exist at the moment.
Doug: Well, thank you so much, Stefano. The Peak is certainly an exciting boot for this year. So congratulations on all the hard work that went into testing, developing, and refining it.
Stefano: Thank you. Ciao. Ciao.
Doug Stenclik is an avid skimo racer and ski mountaineer who lives for sharing the amazing sports of ski touring and splitboarding. Since his first time on skins he was hooked and the obsession has taken him all over the United States and the world pursuing the human powered ski turn. He founded Cripple Creek Backcountry in 2012 and took over the Colorado Ski Mountaineering Race Cup in 2014 to spread knowledge and the love of the sport. In 2019 he took a step back from the ski shop and race promoter life to become a publishing partner with WildSnow.