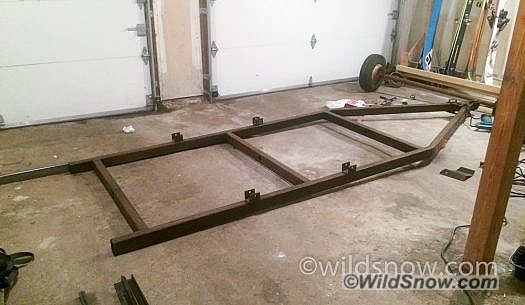
Where it all began. Old rusty frame from a 1972 pop-up camper trailer. Ready for weldin’ and grindin’.
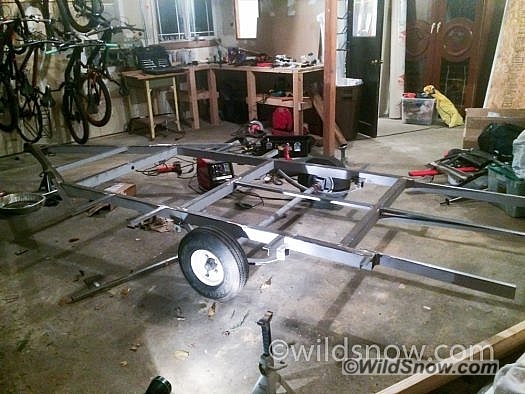
After mods it looked like this, almost ready to paint. I lengthened the frame by welding tubes to the back, and welded chunks of steel angle to the sides for a slight increase in width. I moved the axle rearward as well, to maintain the correct location ratios. I have not drive tested the re-done trailer yet, but the distance between axle and hitch appears to be good for a stable non-whipping tow. Trailer math here for anyone interested.
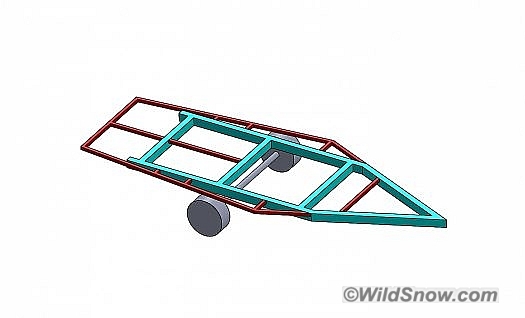
CAD model showing the floor plan. The blue is the original trailer frame, and the red parts are the portions I welded on. It ended up a bit different in real life, but remains similar.
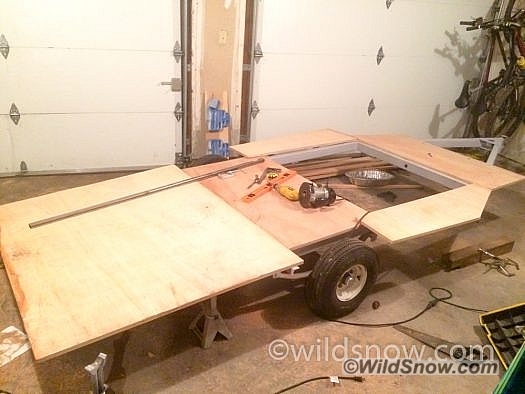
The floor is the only part of this trailer that is susceptible to water damage (it’s the only major wood component). To mitigate the risk I used 3/4 inch marine grade plywood that’s painted with several coats of thinned polyurethane. I also painted the bottom with exterior house paint, and glued the whole thing to the trailer frame with waterproof construction adhesive (it’s also attached with bolts). After the trailer exterior is finished I’ll spray undercoating underneath as another layer of protection.
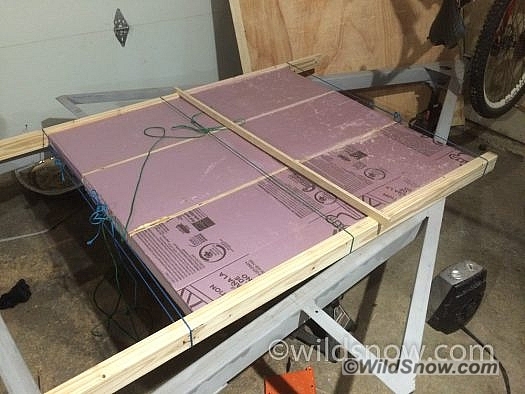
As I was finishing up the trailer frame I began work on the operable drop floor. It’s built out of xps foam and wood, with plywood added to the top and bottom to create a sort of sandwich construction. I covered the whole thing in canvas and glue to increase the durability and waterproofness.
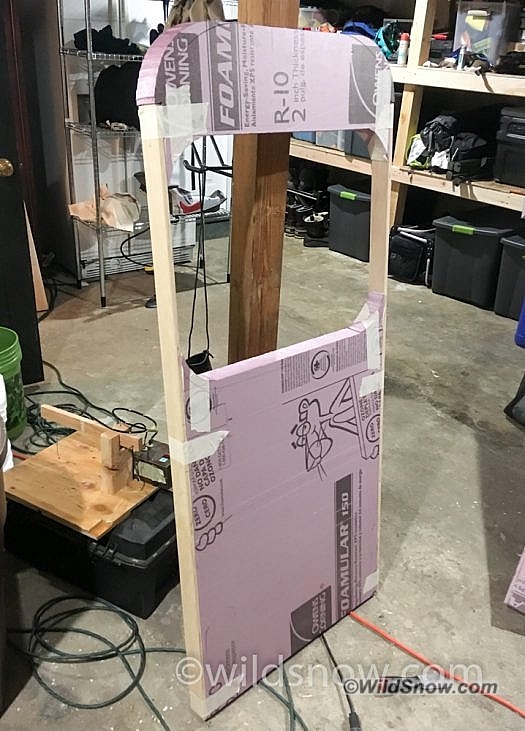
I built the door first, in order to get some practice with the foam and PMF construction. The drop floor construction makes the trailer wall an odd height (~5ft), so a custom door was necessary (I otherwise would have bought one from the RV salvage yard where I got the windows and a few other parts). It’s built out of foam with a minimal wood frame. This makes it exceptionally light and well insulated.
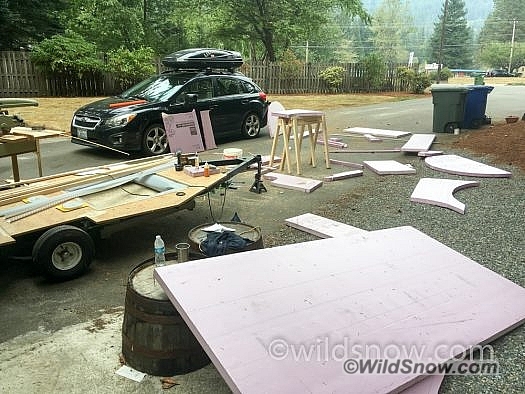
Foam scattered everywhere. Hopefully this isn’t what the highway looks like after the first test drive!
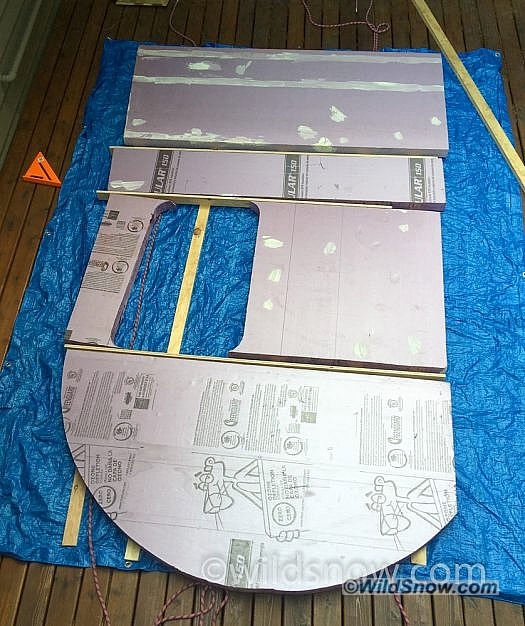
The walls are constructed of several pieces of foam with wood ribs laminated in between. This adds a smidge of strength, while still keeping wood to a minimum, to increase the water resistance and reduced weight. The angles of the hexagonal footprint add strength as well. I will be using this on rough dirt roads, during ski touring access, so the stronger the better.
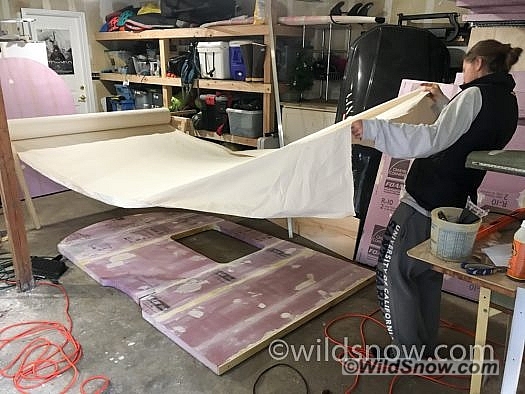
After the wall is glued, we fill divots left by various stages of the construction, and sand smooth in preparation for layering with the canvas and glue PMF.
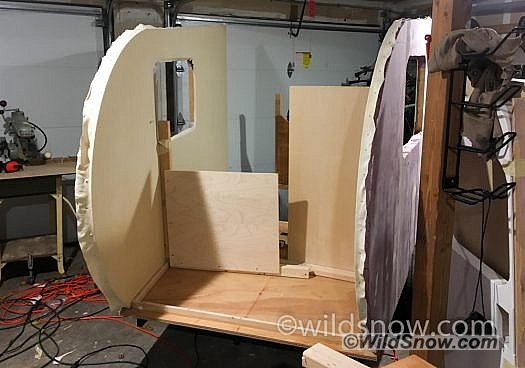
Attaching walls to the trailer floor. The walls are attached to the floor with Gorilla Glue, which is fairly strong and totally waterproof. Once the exterior canvas is applied, it will wrap around the bottom of the trailer floor, adding more strength to the wall-floor bond (no wish to glance in the rear view and see the camper box flying away like a bounce house in a tornado). The sheets of plywood visible in the photo are temporary braces. Due to the flexibility of the foam as well as the hexagonal floor plan, squaring the walls to the floor proved to be challenging. I used everything from trigonometry to “eyeballing” during the process.
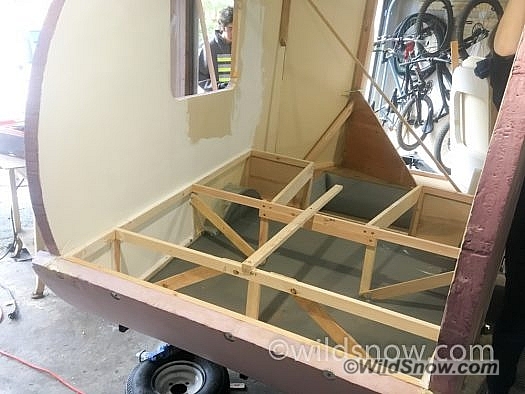
The bed is built with 1×2 wood, to keep it light. The frame is glued and screwed to the foam walls, which adds a significant amount of strength and stiffness to the entire structure.
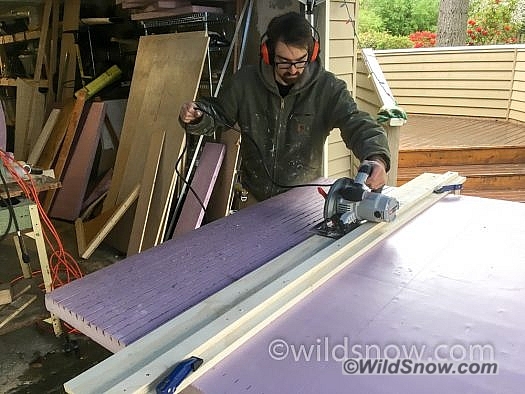
I use a few different methods for cutting the foam. One of the best tricks is to use a smooth edge diamond cutting blade in a circular saw. Since there aren’t any teeth it doesn’t create much dust, but cuts easily; the friction of the blade melts through the foam.
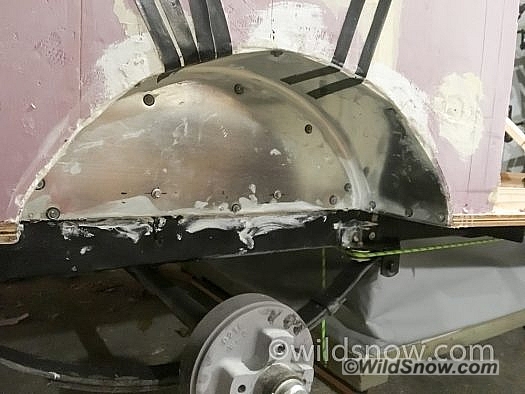
The wheel wells are made from galvanized steel flashing. The visible pulley and cord is part of the drop floor system that raises for ground clearance while accessing locations such as ski touring trailheads.
Louie Dawson earned his Bachelor Degree in Industrial Design from Western Washington University in 2014. When he’s not skiing Mount Baker or somewhere equally as snowy, he’s thinking about new products to make ski mountaineering more fun and safe.