(Editor’s note: Our correspondent Alex is on a press trip in Austria checking out Black Diamond’s skis. We’re excited about this, as the BD ski story has been confusing for consumers due to a preponderance of models and manufacturing venus. Well, it’s all in the old country now, and here are the reports. Oh, and by the way, Alex apparently has yet to try the germknodel.)
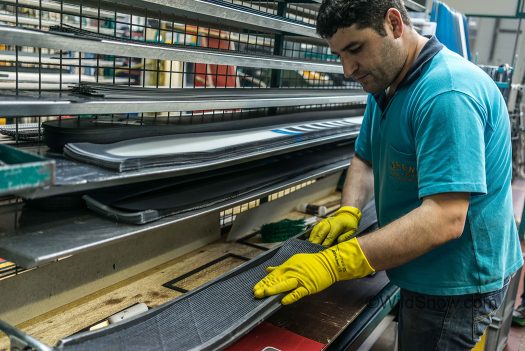
At the Blizzard factory, Austria, each layer of the Black Diamond Helio ski sits on the shelf, a recipe hangs overhead, and the ski mold gets filed with a base, edge, core, carbon, binding plate, and top sheet.
The Alps tower overhead as up to 900 skis a day are born under the watchful and precise eyes methodically buzzing about the Blizzard ski factory in Mittersill, Austria. Founded by a carpenter after the second World War, Blizzard now operates the fourth largest ski factory in the world, producing skis for a number of companies, including for the past three years, Black Diamond.
Walking from the supply racks to the production floor we left the smell of wood and metal, and we’re met by a sweet and sweaty industrial odor. A combination of new car, honey, and glue that made me excited about seeing just how they make the slabs of wood and plastic that give us so much joy.
Over past decades Black Diamond has gone through several iterations of ski manufacturers, first farming out their production to Atomic, and later opening their own factory in China. After concerns over quality, consistency, and production, they have turned here.
After spending a day at the factory, I can say “Handmade in Austria,” is not taken lightly. Black Diamond and Blizzard are now collaborating to make what are clearly some very nice skis.
BD has a big team of folks behind ski product development, but Pete Gompert is the engineer at BD HQ in Utah ultimately responsible for ski design. Pete is a lifelong skier who left work designing turbine parts for jet engines to work for Black Diamond. Pete is both an engineer and a skier through and through. Walking the factory floor, Pete said several times something like, “everything here is just cut perfect!” Pete also skis fast.
Folks like Pete at BD have put a ton of work into their current line of skis – a utilitarian and streamlined response to their older ski lines. The Helio line of ultra-light skis offers something for the ski mountaineer, big days, heavy packs, and long approaches; the Route series is a daily driving mid-weight touring ski; and the Boundary series is a beefier and heavier free ride ski. BD is tweaking the Helio and adding some very cool additions to make their new line a bit more complete for 2018 – more on that soon.
An Austrian mountain guide named Manfred, an engineer named Jorg, at least two Stefans, and a great team of people/skiers at Blizzard connect Pete’s and the BD’s design to the factory floor.
The Blizzard factory office is quiet. Austrian precision lends an austerity to the place — cable knit sweaters, deliberate marches across the room in straight lines, and firm handshakes abound — good old fashion ski stoke still shines through. Skis are everywhere. Manfred’s desk has a full beer stein on it when we walk by and his computer screen is open to a live feed camera at the top of the Kitzbuhel ski area a few miles away. Everyone working in the office is clearly passionate about snow.
Unlike when making skis in Asia, Black Diamond now has local on-the-ground skiers at their production site who can hop on the snow the day after a ski is made. This is not trivial. The caliber of skiers that get out on the boards at each design and production iteration are nothing less than the strongest and best you can imagine: ex World Cuppers and committed free riders, most on planks from the time they took their first steps, all immersed in Austrian ski culture. Yep, there’s a reason good skis are Austrian skis.
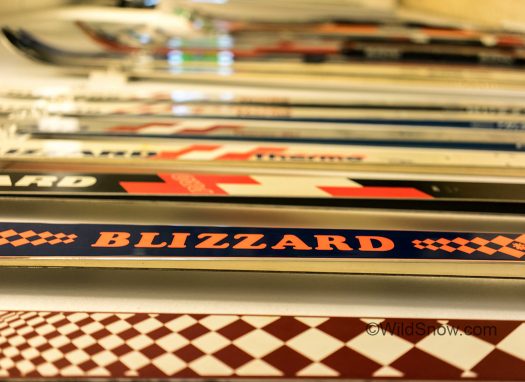
Blizzard has been making skis for more than sixty years, display of older models has palpable spirit.
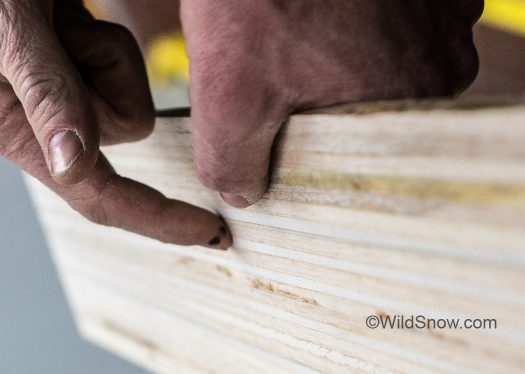
Grains and variety may change, but most often we are still skiing on wood — when we call skis “boards” we are on the mark. This board will become the core of a Helio ski.
Manfred told us that at Blizzard they want to, “give feeling,” to their skis. He and the Blizzard team make sure all the right stuff gets stewed together in the right way for BD, oversee production, and give feedback on issues that show up at the factory.
While big, clean, loud, precise machines guide the process on the factory floor, many hands guide the process. Edges are bent, cores boards are shaped, bases, carbon, and fiber glass are cut. Top sheets are screen printed (or sublimated in some cases).
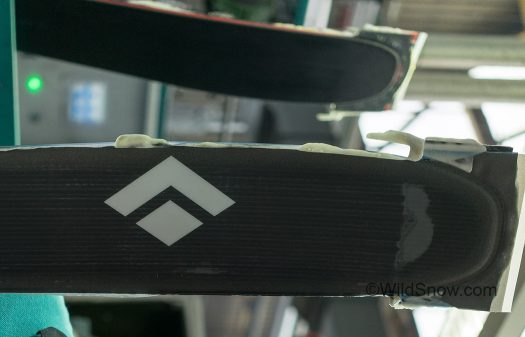
You’ve heard of raw honey and raw sugar, well here is a raw ski! Fresh out of the press, they will be cleaned tunes, inspected, tested, inspected again, paired up and packaged before they hit the snow.
At each step of the process quality control seems really important to Blizzard. In part this protects their bottom line – if they have to reprint a top sheet they lose a couple of bucks, but if they have to remake a whole ski they might lose a couple hundred. Even so, it feels nice to know that so many watchful eyes are looking over the various incubating ski appendages.
BD used to do their own ski durability tests, but by moving to Blizzard, a slew of tests now happen at the factory as part of production. Skis are pressed, slapped, chilled, and worked over to find how they will stand-up to us skiers. One such process oscillates a ski 20,000 times in two hours while the plank is in a cooler – supposedly replicating a two-year life cycle of a ski in just two hours. Thus, the Blizzard built skis appear to really raise the bar on BD quality. While Black Diamond is still an American company designing skis at home, they have infused a little bit of the Alps into their boards.
Black Diamond’s lightest ski, the Helio, has a balsa wood core with alternating horizontal and vertical grains and flax strips, overlaid in construction with carbon fiber and fiber glass, all buttressed by a two-part sidewall — far more high tech and complicated then I would have thought.
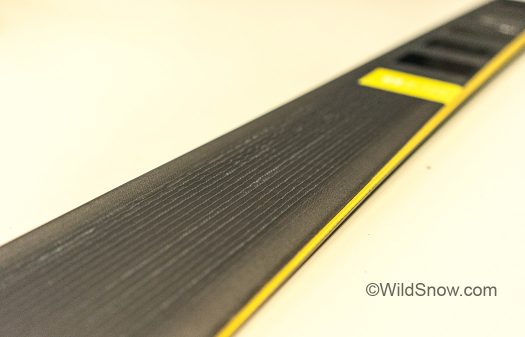
The imperfect grain running down the top of next year’s Helio is the actual carbon in the ski. Real carbon fiber isn’t perfectly straight or symmetrical. Companies often place faux carbon on their top-sheet to market the carbon inside, but the imperfections here are like the ski’s fingerprint, each is unique. I like this.
BD is adding a bit of rubber to the 2018 Helio to help damp the carbon chatter. They are also adding a new ski to the line: Helio 76. I am excited about this ski. It is not a race dimension, but rather a full on spring corn/ski mountaineering/fitness freak/expedition-weight ski (to be offered at 161 and 171 lengths). It will be the same Helio construction, but have a notch for tip skin attachment skis.
Only once the skis are finished at the factory are they paired up — each one married to another that’s as similar as possible. While some margin of error is part of manufacturing, a narrower margin of error allowed within any given pair ensures that each skier’s foot slides the same. Blizzard tests the flex, dimensions, and weight of each ski to find it perfect match.
Black Diamond seems to have found a terrific production match in Blizzard. The factory isn’t in a heartless industrial park in the flatlands, or some smog filled city, but in the Alps – giving their skis a proper mountain birthplace. After visiting the factory, I went skiing – hard to beat. The dumplings might be better in China, but the skis are better in Austria.
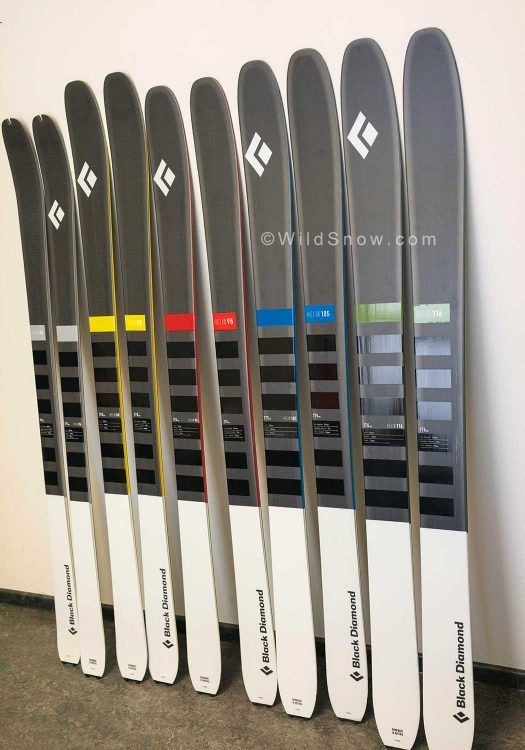
I will be writing up some posts soon on what BD has in store for next season! Here is a preview: the 2018 Helio skis!
Dr. Alex Lee lives in Anchorage, Alaska. Alex is a professor at Alaska Pacific University, teaching philosophy and environmental studies. He also works as a sometimes guide, naturalist, writer, and photographer.