On my way up to school in Bellingham, Wa, I swung buy the CiloGear backpacks factory and office. Located in a huge building that used to be the Columbia Sportswear factory, it took a while to find. The factory is a backcountry gear head’s dream, filled to the brim with packs, prototypes, and various high tech fabrics. (Previous post about CiloGear)
Cilogear was started in Turkey by Graham Williams, and then moved to New York, then to Portland, where it now resides. CiloGear makes well designed packs made from various long-lasting fabrics. His highest quality are made from 100 percent Dyneema, a super durable fabric that is 40 percent stronger than steel. These sacks are simple, durable, and built to last — all qualities I’ve learned to love in a backpack, and what we want on Denali this spring. The packs are also super customizable, as all the straps and many of the other features can be removed, reducing the weight a ton. A great idea, as I always end up chopping stuff off any pack I get.
We are indeed planning on taking a variety of CiloGear Dyneema packs to Denali. By doing so, we can have backpacks with plenty of volume so packing is easy, but they’ll weigh quite a bit less than an equivalent pack made with normal fabrics which have to be heavier and thicker. More, as mentioned above, CiloGear packs area easily stripped of extra weight, so that helps as well in comparison with packs that have so many straps and buckles they look like something out of a science fiction movie.
To keep costs down, Graham makes packs when orders come in, rather than keeping a stock of packs on hand. He says his crew can make most packs in under two hours. He speeds up the process by sewing together various parts ahead of time that work for a variety of packs and sizes. He keeps a supply of these on hand, ready to be assembled into full backpacks when the orders come in.
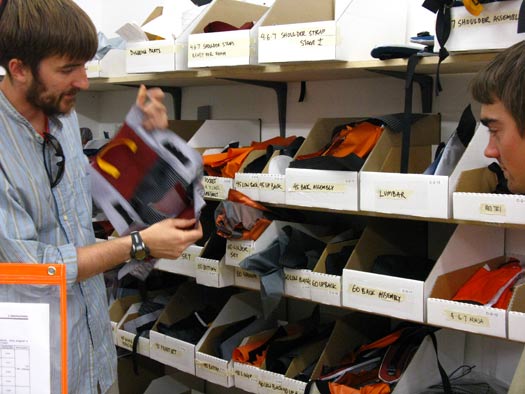
Bins stocked with Dyneema pack parts
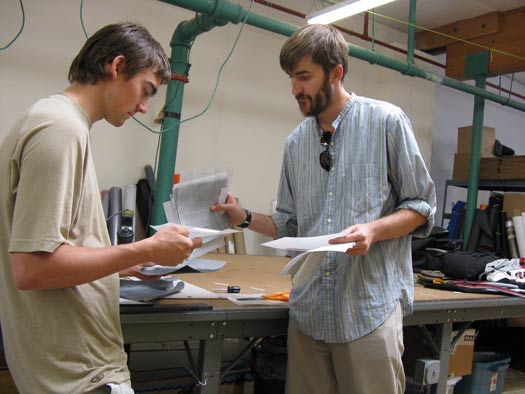
Checking out some samples of high tech fabrics. One felt almost like tissue paper to the touch, but I couldn't tear it, no matter how hard I tried.
CiloGear packs are used by many world class alpinists, who’s old test packs are scattered around the place. Many of them have withstood amazing abuse without ripping. One was used as a weight tied to the ends of a rap rope to keep them from tangling on a descent of some huge wall in the Himalayas. It only had a few tiny holes.
It is sweet to see a small company making a quality product that just works on a small, sustainable scale.
Louie Dawson earned his Bachelor Degree in Industrial Design from Western Washington University in 2014. When he’s not skiing Mount Baker or somewhere equally as snowy, he’s thinking about new products to make ski mountaineering more fun and safe.