Tech Tuesday is recurring segment sponsored by Dynafit to get you in the right touring gear and make sure you know how to use it.
Things to consider when choosing your next climbing skin
Sunlight breached a thin cloud cover as dawn broke on the mountain ridge. The crisp air hinted at how cold the new snow had blown in the night before. Better yet, I was out with a crew that was ready to hammer all day and we had vast miles of new terrain to explore. I careened down the first run, breathless between exalted squeals. Forgetting all protocol while transitioning, I stepped out of my binding and immediately plunged up to my thigh in deep powder. No matter. Instead of getting frustrated, I reached into my jacket to pull out my climbing skins and begin the race uphill.
But the skins weren’t ready to race uphill. No, the old skins I’d grabbed that morning were frozen and icy with no chance of staying on my skis. I was in for a long day, I realized. My trusted old friends and companions on tour after tour had finally had enough.
Climbing skins are likely the most underrated piece of ski touring setups. They are typically an afterthought to the always sexy and critical boot, binding and ski decisions. But they’re the crucial contact point with the snow for the majority of time you spend traveling up a mountain. You would never see a cyclist throw down for a new bike frame with shiny and smooth components and then grab bent wheels, rotten tires and patched up tubes to take the rig out for its inaugural spin. Yet we see this all the time in the world of human-powered skiing. I have even done it myself and ruined more days in the mountains than I care to admit!
The true value of skins is just the first misconception many users have about them. Here are five more commonly held beliefs about skins, along with evidence to bust them and tips gathered from real WildSnow trial and error.
1. Beginners should use 100% Nylon skins
I have seen this myth floating around on the internet for years because of the generalization “if you need grip go Nylon and if you want glide go Mohair.” It’s particularly been played to beginners who need more grip to compensate for the technique they haven’t developed. Yet, there are few ski tourers out there using 70% mohair/30% nylon skins that ever complain about grip on the skin track.
An analogy: there was a time before tech binding acceptance when the myth of the plate binding flourished. The thinking was that if you wanted a binding that skied “hard,” it needed to be heavy and have a plate. After decades of tech binding innovation resulting in the final approval and commitment of alpine brands like Marker and Salomon to the “new system,” that myth has been laid to rest.
Think of nylon as the plate bindings of the skin world. In very select applications it’s appropriate, but more often, a skin with mohair will prime you for efficiency and success. A 70% mohair/30% nylon or even a 100% mohair skin is sufficient for climbing the steepest of mountains. Getting the most out of mohair may require you to tune your skinning technique, but that’s hardly a bad thing. Whether you’re a beginner or seasoned pro, better technique will work to increase your uphill efficiency overall, no matter what kind of skin you’re on.
This isn’t so say nylon climbing skins are completely defunct. The material is durable, for instance, and doesn’t retain as much water on wet days as mohair. However, a 100% nylon skin packs down poorly and feel incredibly slow on a skin track. Last winter, I had forgotten my climbing skins and was forced to use a nylon set. The difference was palpable. I traded the friend I was with for one of his blended skins so we could do a side by side comparison. On my left ski, the Dynafit skin by Pomoca 70/30 mix felt effortless on each stride; on the right, a full orange nylon skin felt like I was dragging my ski across sandpaper.
2. You need edge to edge coverage on your powder skis
As some WildSnow readers will testify, skis used to be a lot skinnier. Now that the average width of an “all mountain” touring ski is closer to 100mm there is far more grip to go around. Try this: hold your skis together at the waist and look to see where your new rocker tips diverge from each other. Measure the width of the contact point and subtract 6mm to leave the edge exposed. If your uncut skins are as wide as this measurement, that’s fine.
Of course, fully covering your rocker shovel that will rarely ever touch the snow won’t slow you down significantly. It will, however, add a negligible amount of weight to each step and slightly less glide on your stride, especially while breaking trail. Use this rule of thumb: the more base material showing when cut your skins, the easier it will be to center your skins and increase your overall glide.
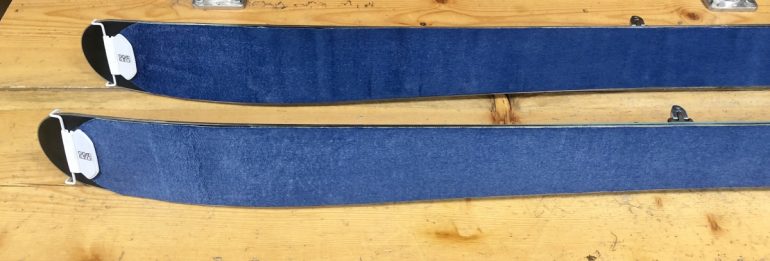
Nothing wrong with wall to wall carpet as seen here, but as your ski gets wider it may be more drag on the snow, especially when breaking trail.
3. All ski manufacturers make climbing skins
The call of a pair of pink Black Crows skins to match your pink highlighter Black Crows ski may, in fact, be more than one person can resist. But be aware: although they are a perfect match, Koch Alpin in Austria, not Black Crows is behind this clever rebranding. In many cases a skin being rebranded and sold as a package with the ski could be the exact right tool for the job, but sometimes it can lead you astray.
These days, hundreds of models of skins are available to coordinate with all the new touring skis, but many are just different patterns with different logos printed on the bottom. There are really only a few big skin manufacturers. The biggest companies –– G3, Pomoca, Black Diamond, Contour and Coletex –– make skins for the majority of companies who rebrand them, while there are a few other small companies out there doing it for themselves. Pomoca alone makes skins for the following: Dynafit, Jones, K2, Dynastar, Rossignol, Blizzard, Voile, Movement, Solomon, Faction and more.
When choosing skins, the priority is to pick a brand based on glue and plush, and then consider tip and tail attachment preferences. The glue for a skin manufacturer stays relatively consistent between different models and rebranding. It is the plush side and the way the treatments placed on the skin that makes up most of differences. Only as a finishing touch should you worry about whether the logo matches your brand of skis.
4. Re-gluing climbing skins will save you money
What a bummer! My skis are leaving glue on the bottom of my skis but everything else on the setup is perfect. I know, it’s tempting to buy a couple tubes of glue and set to work reviving your skins. While skins can certainly be touched up by adding glue, a full re-glue of a hacked pair of skins is a dirty job. You must first entirely strip off the old glue before adding the new layer. This entails superheating a scraper to a dangerous level, which then makes the glue molten to the touch or vaporous to the lungs. The corresponding smoke that fills the room is definitely not the fun kind.
Sure, you could hire a shop to do this, but it won’t save you that much money. Throughout my years working on benches around the country, I’ve found it’s nearly impossible to offer this service for less than $100. With $50 for supplies, a couple tubes of glue and hours spent, you could probably find a pair on sale for less.
Just because you can’t effectively pay someone else to do your dirty work doesn’t mean there isn’t a DIY approach. If cracking a beer in your garage and huffing chemicals for a few hours sounds like a good time (it has for me on more than one occasion), go for it. But, keep in mind that the new glue may not last as long as the factory laid glue and therefor you may see it fail in the field faster. This method should only be employed on its merits of reducing waste and not on cost savings alone. (See our step-by-step from the archives if you want to know more.)
5. Climbing skins will last the lifetime of your setup
Again, think about skins like the tires on those summer devices a.k.a. bikes designed to hold us over until the ground is white again. If you let the rubber decay until it is hard and brittle or thin and bald, you are going to spend your rides flatting, slipping out and getting angry.
$200 seems like a lot for a piece of faux animal fur with glue on the back, but each day out in the mountains in priceless. If you consider your ski touring setup to be composed of skis, bindings, boots and skins, skins are the least expensive component. With decent care (more on that in a future Tech Tuesday), you should be able to get almost 100 days before seeing performance begin to drop off. The extra $2 per day you can eke out of an old pair will rarely be worth the ultimate headache of ski touring known as skin failure.
Back to my powder day fail: it was not from lack of experience that I pulled that old pair of orange skins out of a dusty covered crawl space bin that should have been left for archaeologists to study the primitive ski tourer in decades to come. They did, after all, fit my new skis perfectly. I spent the rest of that epic powder day slopping up kickturns and then lagging behind my partners with bulging base layers and skin glue tearing at my chest hair, trying desperately to coax my skins into one last lap. Some people just have to fail to learn, and it seems I’m one of them.
Doug Stenclik is an avid skimo racer and ski mountaineer who lives for sharing the amazing sports of ski touring and splitboarding. Since his first time on skins he was hooked and the obsession has taken him all over the United States and the world pursuing the human powered ski turn. He founded Cripple Creek Backcountry in 2012 and took over the Colorado Ski Mountaineering Race Cup in 2014 to spread knowledge and the love of the sport. In 2019 he took a step back from the ski shop and race promoter life to become a publishing partner with WildSnow.